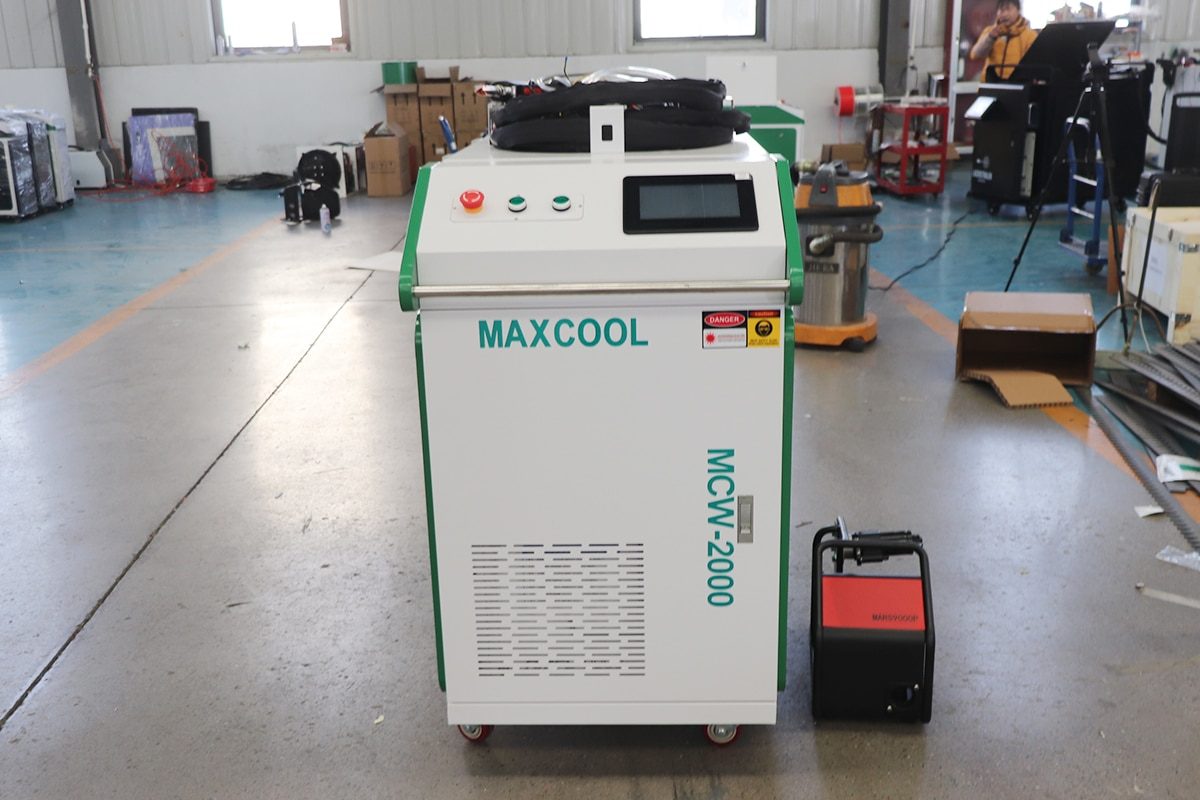
Autogenous VS Filler Laser Welding
Laser welding is a high-precision joining process widely used in industries such as automotive, aerospace, electronics, and medical manufacturing. It offers deep penetration, narrow welds, low distortion, and high-speed operation. Within this process, two main techniques are commonly used: autogenous laser welding and filler laser welding. While both rely on a concentrated laser beam to melt and fuse metal, they differ significantly in their approach and suitability for specific applications.
Autogenous laser welding joins metals without any added material. It depends solely on melting the base metals, making it highly efficient for joints with tight fit-up, low gap tolerances, and materials of similar composition. This method is ideal when minimizing contamination, maintaining joint aesthetics, or reducing processing time is a priority.
Filler laser welding, on the other hand, uses a wire or powder filler material to bridge gaps, compensate for joint misalignments, or modify the weld’s mechanical properties. It provides greater flexibility in joint design and is essential when welding dissimilar metals, thicker sections, or parts prone to cracking.
Choosing between autogenous and filler laser welding depends on the specific material, part geometry, mechanical requirements, and production goals. This article explores both methods in depth to clarify their advantages, challenges, and ideal use cases.
Table of Contents
What is Autogenous Laser Welding
Autogenous laser welding is a high-precision welding method where two metal parts are fused together using only a laser beam, without the use of filler material. This method relies entirely on melting the base materials at the joint interface to create a weld. It is most effective when the materials being joined are similar in composition and thickness, and when the joint fit-up is tight and consistent. This technique is especially valuable in clean, controlled manufacturing environments where minimal contamination and consistent weld quality are essential.
Working Principle
The laser beam, typically generated by fiber lasers, is concentrated onto the joint area with high energy density. This localized energy input melts the surface edges of the base materials. As the beam travels along the joint line, the molten pool cools and solidifies, forming a metallurgical bond. The depth of penetration and weld geometry depend on several factors, including laser power, focus spot size, welding speed, and material type. Since no additional material is introduced, the weld pool must be carefully controlled to avoid defects like underfill or cracking.
Autogenous welding works best in keyhole mode, where the laser creates a vapor cavity in the molten metal, allowing deep and narrow welds. This is advantageous for achieving strong joints in thin sections or hard-to-reach areas.
Features
- Narrow Weld Bead: Produces fine, clean welds with minimal width and depth variation.
- Low Heat Input: Results in a small heat-affected zone (HAZ), which helps maintain mechanical properties of the base metal.
- No Material Alteration: Since no filler is added, the weld metal retains the exact composition of the parent materials.
- Automation Friendly: Easily integrated into robotic systems for high-speed, repeatable production.
- Non-Contact Process: The laser never physically touches the workpiece, reducing tool wear and contamination risk.
Advantages
- Cost-Effective for High-Volume Production: Eliminates filler materials and simplifies supply logistics.
- Superior Weld Cleanliness: No flux or filler means fewer impurities or inclusions in the weld.
- High Accuracy: Suitable for micro-welding and parts with complex geometries or small tolerances.
- Minimal Distortion: Low thermal impact reduces warping or deformation, crucial in precision parts.
- Excellent Aesthetics: Produces a visually smooth, uniform weld with little to no post-processing.
Limitations
- Requires Perfect Fit-Up: Any gap or misalignment between parts can lead to incomplete fusion or weld defects.
- Limited Use with Dissimilar Materials: Since it depends on uniform melting behavior, it’s less effective with metals of differing melting points or thermal conductivity.
- No Gap Bridging: Cannot compensate for gaps, poor part tolerances, or joint inconsistencies—making part preparation critical.
- Risk of Cracking in Certain Alloys: Materials with high thermal expansion or those prone to solidification cracking (like aluminum or some stainless steels) may be difficult to weld autogenously without special controls.
Applications
- Automotive: Used for precision welding of gears, valves, sensors, injector components, and structural brackets.
- Aerospace: Applied to lightweight structures, fuel lines, and titanium components requiring strength and minimal added weight.
- Medical Devices: Common in stainless steel or titanium surgical tools, pacemaker housings, and implantable components, where contamination-free, high-strength joints are critical.
- Electronics: Utilized in the fabrication of micro-batteries, sensor housings, and small metal enclosures where heat sensitivity is a concern.
- Watchmaking and Jewelry: Ideal for clean, detailed welding of fine metal parts with high visual and structural standards.
What is Filler Laser Welding
Filler laser welding is a laser-based welding process that uses an external filler material—typically in the form of wire or powder—in addition to the base metals. The laser melts both the base metal and the filler to form a joint. This method is used when parts don’t fit perfectly, when dissimilar materials are involved, or when enhanced joint properties are required.
Working Principle
In filler laser welding, a high-intensity laser beam is directed at the weld joint, just like in autogenous welding. However, at the same time, filler material is fed into the weld pool. The laser simultaneously melts both the filler and the edges of the base material, allowing them to mix and form a metallurgical bond upon solidification.
The filler is usually added via a wire feeder positioned at a specific angle to the laser beam. The interaction of laser power, wire feed rate, travel speed, and shielding gas determines the quality and characteristics of the weld. This method can be used in both conduction and keyhole modes, depending on penetration depth and application.
Features
- Filler Material Input: Allows precise control over weld composition and reinforcement.
- Gap Bridging Capability: Can handle joint gaps, misalignments, or poor fit-up better than autogenous welding.
- Enhanced Joint Strength: Suitable for joints requiring mechanical reinforcement or increased ductility.
- Flexible for Complex Joints: Works well with variable joint geometries and multi-pass welds.
- Supports Alloy Modification: Filler can be tailored to improve corrosion resistance or reduce cracking risk.
Advantages
- Improved Weld Quality on Imperfect Joints: Filler material helps fill gaps and compensate for dimensional tolerances.
- Welding Dissimilar Metals: Enables joining of metals with different melting points or thermal expansion rates.
- Reduced Cracking Risk: Filler can lower hardness and residual stress in the weld zone, reducing susceptibility to hot cracking.
- Customizable Metallurgy: The ability to select filler composition allows for stronger, tougher, or more corrosion-resistant welds.
- Better for Thicker Sections: Supports deeper welds and multiple layers for structural applications.
Limitations
- More Complex Setup: Requires additional equipment (wire feeder, precise angle control, etc.) and process parameters to manage.
- Slower Than Autogenous Welding: Additional material and handling reduce overall speed.
- Higher Cost: Uses consumables (filler wire or powder) and may require more post-processing.
- Increased Heat Input: Can lead to a larger heat-affected zone and more distortion if not properly managed.
- Greater Operator Skill Required: More variables must be controlled to avoid defects like porosity or inconsistent bead shape.
Applications
- Aerospace: Welding of critical load-bearing structures, often with dissimilar alloys or where strength must be optimized.
- Automotive: Used for chassis components, transmission housings, and crash structures where filler provides added strength.
- Shipbuilding and Rail: Applied in large structures requiring thick-section welds and tolerance to joint variation.
- Tool and Die Repair: Filler welding is used to rebuild worn surfaces or modify existing tools with precision.
- Power Generation and Pipelines: Ideal for thick-walled components, pressure vessels, and piping where structural integrity is key.
Key Differences Between Autogenous and Filler Laser Welding
The decision to use autogenous or filler laser welding depends on the specific requirements of the part being welded—material behavior, design tolerances, performance expectations, and production goals. Below is a detailed breakdown of how the two methods differ across five critical parameters:
Material Type and Thickness
- Autogenous Laser Welding: Works best with homogeneous materials that have similar melting points and thermal properties, such as stainless steel, titanium, and nickel alloys. It’s particularly effective for thin-walled components (typically under 3 mm) where deep penetration and low distortion are desired. However, it’s less reliable when welding dissimilar metals, as differences in melting temperature and thermal expansion can lead to defects or weak joints.
- Filler Laser Welding: Offers broader versatility across materials, including dissimilar metal combinations (e.g., stainless steel to carbon steel, or aluminum to magnesium) and thicker sections where more material volume must be fused. The filler can be chemically matched to balance differences in metallurgy and compensate for potential cracking issues. It also allows for welding of hard-to-weld or crack-sensitive alloys, such as aluminum-silicon or high-carbon steels.
Gap Size and Joint Fit-Up
- Autogenous Laser Welding: Requires tight tolerances and excellent joint preparation. Any gap larger than 0.1 mm can lead to poor fusion, porosity, or lack of penetration. It is most effective when parts are machined precisely and held in stable fixturing, making it ideal for controlled, repeatable environments.
- Filler Laser Welding: Can accommodate larger gaps and slight misalignments due to the presence of filler material. It’s ideal for applications where perfect fit-up is not feasible, such as in large assemblies or field repairs. The filler also helps maintain weld continuity even with joint geometry variation, such as bevels, gaps, or corners.
Mechanical Requirements
- Autogenous Laser Welding: Delivers good mechanical strength when the base metals are compatible and the joint is properly prepared. However, the lack of filler material means there’s limited control over the metallurgical structure of the weld. In highly stressed or fatigue-sensitive applications, this may be a limiting factor.
- Filler Laser Welding: Allows for customization of the weld metal’s composition, making it possible to improve mechanical performance beyond what the base materials alone provide. This includes enhanced tensile strength, fatigue resistance, and ductility. It’s preferred in critical structures, such as aerospace frames or pressure vessels, where joint performance is non-negotiable.
Production Speed and Complexity
- Autogenous Laser Welding: Offers faster cycle times and simpler process control. There’s no need to synchronize filler feed, reducing setup and programming complexity. It’s highly suited to automated production lines where speed, repeatability, and low heat input are crucial.
- Filler Laser Welding: Involves more variables—wire feed rate, angle, laser-filler interaction—which can slow down the process slightly and require more skilled setup. However, for complex assemblies or variable geometries, filler welding provides the adaptability needed to maintain consistent quality.
Cost Constraints
- Autogenous Laser Welding: Generally more cost-efficient, especially for high-volume production of small, precision parts. Eliminating filler reduces material and inventory costs, and the process itself is quicker and requires less post-processing (e.g., grinding or cleaning). Ideal when tight part tolerances and clean conditions are already in place.
- Filler Laser Welding: Comes with higher upfront and operational costs—consumables (filler wire), extra process controls, and potential increases in post-weld cleanup. However, it can save cost in rework and scrap when welding imperfect parts or complex assemblies. In many cases, filler welding is the only viable solution for high-integrity or dissimilar-metal joints, making the cost justified.
Considerations When Choosing Autogenous and Filler Laser Welding
Choosing between autogenous and filler laser welding involves more than selecting a process—it’s about aligning the welding method with the realities of material behavior, design tolerances, joint performance, and production economics. Each application presents different challenges, and understanding these core considerations can help ensure weld quality, process efficiency, and long-term reliability.
Material Type and Thickness
Autogenous Laser Welding
Best suited for metals with similar chemical composition and thermal properties, such as stainless steels, nickel-based alloys, and titanium. Works particularly well with thin sections (usually < 3 mm) because the heat input is concentrated and the weld pool is small, minimizing distortion and burn-through. However, this method has limited effectiveness when dealing with materials prone to solidification cracking or differing melting points.
Filler Laser Welding
The more adaptable choice when working with dissimilar metals (e.g., stainless steel to mild steel, or aluminum to magnesium) or thicker cross-sections (above 3 mm). Filler material helps balance differences in thermal expansion, melting temperature, and chemical compatibility. It’s also useful when welding alloys sensitive to cracking, as specific filler compositions can reduce brittleness and enhance joint ductility.
Required Welding Properties
Autogenous Laser Welding
Ideal when welds must be clean, cosmetically precise, and free of contaminants. Since no filler is added, the weld retains the exact composition of the base metal, which is critical in regulated industries like medical or semiconductor manufacturing. Also advantageous when a minimal heat-affected zone (HAZ) is required to preserve mechanical or microstructural properties near the weld.
Filler Laser Welding
Offers more control over the mechanical and metallurgical properties of the joint. The filler metal can be selected to:
- Match or enhance the strength of the base material
- Improve fatigue performance in cyclic-loading environments
- Increase toughness in brittle alloys
- Improve corrosion resistance in aggressive service conditions
This makes it the preferred option for safety-critical or load-bearing components.
Cost Considerations
Autogenous Laser Welding
More cost-effective in high-volume, tightly controlled production where joint gaps are minimal and parts are consistently manufactured to specification. It eliminates filler material costs, simplifies process setup, and often reduces post-weld cleanup due to cleaner weld profiles. It’s an efficient choice for small, precision parts where even minor savings per part add up.
Filler Laser Welding
Involves higher consumable costs (wire or powder), added process complexity, and potentially slower cycle times due to the need for filler feeding and tighter control over process variables. However, it may result in lower rejection rates and less rework in situations where joint variability or complex geometries are present. Over time, it can be more economical in applications where weld integrity is critical and defects are costly.
Application-Specific Requirements
Autogenous Laser Welding
Common in industries where parts must meet stringent cleanliness and dimensional tolerances, such as:
- Medical devices: Implants, surgical tools
- Electronics: Battery cases, sensors
- Precision automotive parts: Fuel injectors, valves
- Aerospace components: Thin-walled brackets, tubing assemblies
Autogenous welding is also easier to integrate into automated production lines where part geometry and joint conditions are consistent.
Filler Laser Welding
Essential for applications involving variable joint conditions, thicker sections, or parts that must handle high mechanical loads or thermal cycling. It’s widely used in:
- Aerospace: Turbine housings, structural frames
- Automotive: Transmission cases, crash structure welds
- Energy sector: Pressure vessels, heat exchangers
- Tool and die industries: Repair and buildup welding
Filler welding is the go-to method when flexibility and weld strength are prioritized over speed.
Ultimately, the choice between autogenous and filler laser welding comes down to fit: matching the process to the material behavior, joint design, mechanical requirements, and cost targets of the application. In tightly controlled environments with precise part fit-up, autogenous welding is highly efficient. In complex or demanding scenarios, filler welding provides the adaptability and strength needed to ensure long-term performance.
Summary
Autogenous and filler laser welding are two distinct approaches to achieving high-quality, high-precision welds, each suited to specific applications and manufacturing conditions. Autogenous laser welding, which uses only the base materials to form the joint, is ideal for thin sections, tight fit-up, and applications requiring clean, fast, and repeatable welds. It offers advantages in terms of speed, cost, and minimal heat input, making it well-suited for industries such as medical device manufacturing, electronics, and precision automotive components.
Filler laser welding, on the other hand, introduces a filler material into the weld pool, offering greater flexibility. It accommodates wider gaps, allows welding of dissimilar or thicker materials, and enables fine-tuning of mechanical properties. This makes it essential for demanding applications in aerospace, heavy machinery, structural components, and repair work where joint integrity and strength are critical.
Choosing between the two methods depends on several factors: material type and thickness, mechanical performance requirements, joint condition, and cost targets. While autogenous welding excels in controlled, high-speed environments, filler welding provides the adaptability needed for more complex or variable conditions. Understanding the strengths and limitations of each method is key to selecting the most effective and reliable welding solution.
Get Laser Welding Solutions
At Maxcool CNC, we specialize in delivering intelligent laser welding solutions tailored to your production needs. Whether you’re working with tight-tolerance components requiring clean, high-speed autogenous welding or tackling more complex joints that demand the versatility of filler-assisted welding, our advanced laser systems are built to perform with precision, reliability, and efficiency.
Our equipment supports a wide range of materials and applications, from micro-welding of medical devices to heavy-duty structural welding in automotive and aerospace. With customizable configurations, automated integration options, and user-friendly interfaces, Maxcool CNC systems help manufacturers achieve consistent weld quality, reduce cycle times, and minimize downtime.
Not sure which welding method is right for your application? Our team of laser welding experts is here to provide technical consultation, sample testing, and process development support. We’ll help you select the optimal solution based on material type, joint design, mechanical requirements, and production goals.
With Maxcool CNC, you don’t just get a machine—you get a partner in advanced manufacturing. Contact us today to explore how our laser welding solutions can improve your process, boost quality, and lower production costs. Let us help you weld smarter.