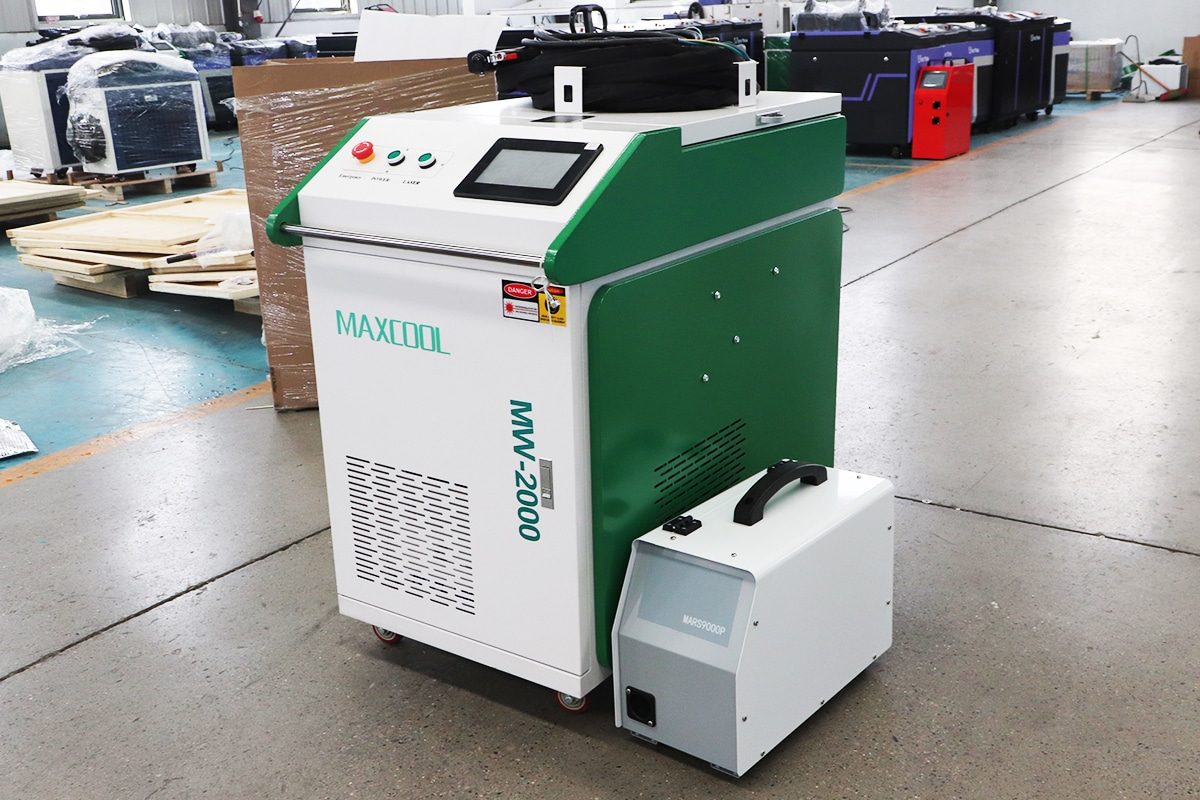
Fundamentals of Laser Welding
How Laser Welding Works
Laser Sources and Process Modes
Several types of lasers are used in welding, each with unique properties:
- Fiber lasers: High efficiency, excellent beam quality, suitable for fine or deep welds.
- Disk lasers: Similar to fiber lasers, with good thermal management and high power.
- CO2 lasers: Higher wavelengths, suited for non-metallics and thicker sections, but limited by beam delivery constraints.
- Nd:YAG lasers: Versatile, especially for pulsed welding or hybrid processes.
Advantages and Design Implications
Laser welding’s key advantages include:
- High speed and productivity: Reduces cycle times.
- Low heat input: Minimizes thermal distortion and residual stress.
- Non-contact process: Allows access to tight or delicate areas.
- Precision and repeatability: Ideal for automated systems and high-spec applications.
The Role of Joint Design in Laser Welding
Key Design Considerations
- Joint Geometry: Butt joints are ideal for thin materials and high-strength welds but require precise alignment. Lap joints offer ease of assembly and higher tolerance for misalignment, but can lead to undercuts or porosity if not carefully controlled.
- Fit-Up and Gap Control: Laser welding tolerates minimal joint gaps—typically less than 0.1 mm. Larger gaps result in inconsistent welds or incomplete fusion. High-precision machining and fixturing are essential.
- Material Properties: Thermal conductivity, reflectivity, and alloy composition influence joint design. Aluminum and copper, for example, require special attention due to their high reflectivity and thermal dissipation.
- Access and Beam Delivery: The joint must be accessible to the laser beam, which typically travels in a straight line. Complex geometries may require beam steering, multi-axis systems, or hybrid techniques.
Design for Functionality and Manufacturability
Joint Types and Geometries
Butt Joints
Lap Joints
T-Joints
Corner and Edge Joints
Fillet Welds and Hybrid Configurations
Material and Metallurgical Considerations
Base Metal Selection
Dissimilar Metal Welding
Thickness Mismatch Strategies
Microstructural Effects and Mitigations
Laser welding’s rapid thermal cycle affects grain structure, hardness, and phase transformations. In carbon steels, this can lead to martensitic zones and increased brittleness. In aluminum alloys, solidification cracking and porosity are common. Mitigation strategies include:
- Preheating or post-weld heat treatment
- Controlling cooling rates with optimized parameters
- Using filler alloys to modify weld chemistry
- Surface treatments to improve absorption and fusion quality
Fit-Up Requirements and Tolerances
Gap Control
Alignment, Fixturing, and Clamping
Accurate alignment of components ensures proper energy delivery and consistent weld depth. Any mismatch or movement during welding can cause beam deflection, variable penetration, or weld defects. Fixturing systems must:
- Hold components securely without distortion
- Ensure repeatable positioning
- Allow unobstructed beam access
Beam Focus and Manipulation
Penetration, Fusion Zone, and Weld Bead Geometry
Keyhole VS Conduction Modes
Laser welding operates in two primary thermal modes:
- Conduction Mode: Occurs at lower power densities. The laser heats the surface, and heat flows into the material by conduction. This results in shallow, wide welds with smooth surfaces and low distortion. Ideal for thin materials or aesthetic welds where strength demands are low.
- Keyhole Mode: Achieved at higher power densities. The laser vaporizes the material, creating a deep, narrow cavity (keyhole) that allows the beam to penetrate deeply. This mode produces high aspect ratio welds—narrow but deep—ideal for structural joints requiring strength and full penetration.
Aspect Ratio and Weld Profile
The weld profile (cross-sectional shape) should match the joint’s mechanical load conditions:
- A convex profile may increase fatigue life, but can also concentrate stress.
- A flat or slightly concave profile typically minimizes stress risers and improves load distribution.
- Undercuts or excessive reinforcement should be avoided through precise parameter control and beam alignment.
Heat Input Management
Laser welding offers a low overall heat input, which is a key advantage. However, localized overheating or underheating can still occur:
- Too much heat can cause burn-through, distortion, or metallurgical changes (e.g., grain coarsening, brittleness).
- Too little heat results in incomplete penetration, poor fusion, or lack of bonding.
Shielding Gas, Backing, and Assist Gas Design
Shielding Gas
Shielding gas is directed over the weld zone to prevent atmospheric contamination during welding. Its main functions are:
- Preventing oxidation of the molten metal.
- Stabilizing the weld pool.
- Enhancing arc and beam coupling, depending on the gas type.
Common shielding gases:
- Argon: Most widely used due to its inert nature. It provides excellent protection and is suitable for most metals.
- Helium: Offers deeper penetration and higher heat conductivity, but is more expensive. Often used in combination with argon.
- Nitrogen or CO2 (less common): Sometimes used with specific steels, but can introduce porosity or alter metallurgy if not properly controlled.
Design Considerations:
- Use laminar flow to avoid turbulence and protect the molten pool.
- Shielding nozzles should be positioned close to the weld with a proper angle to cover the full fusion zone.
- Flow rates must be balanced—too low allows contamination; too high can cause turbulence and suck in air.
Backing Gas
Applications:
- Used in butt welds and pipe or tube welding where root shielding is essential.
- Often delivered via a purge box, trailing shoe, or inert chamber.
- Gases Used: Typically argon or nitrogen, depending on material sensitivity.
Design Tips:
- Ensure full coverage and controlled flow to prevent air ingress.
- Consider using diffusers or flow restrictors for even distribution.
Assist Gas
Examples:
- Oxygen or compressed air can enhance keyhole welding on carbon steel, aiding penetration.
- Nitrogen or argon can help with spatter control or oxide prevention.
Design Factors:
- Nozzle shape, pressure, and angle must be tuned for each application.
- Improper use can cause surface defects or interfere with the laser beam.
Thermal-Mechanical Analysis and Distortion Control
Heat Flow Modeling
Accurate modeling of heat transfer is the foundation of thermal analysis in laser welding. Heat flow is affected by:
- Laser power and beam profile
- Material thermal conductivity and specific heat
- Weld travel speed and focus depth
- Joint geometry and thickness
Finite Element Analysis (FEA) is commonly used to simulate:
- Temperature distribution over time (thermal cycle)
- Melt pool size and shape
- Cooling rates and solidification patterns
Residual Stresses and Distortion Mitigation
As the welded material heats and cools rapidly, it expands and contracts unevenly, generating residual stresses. These internal stresses can lead to:
- Distortion or warping of thin or unsupported sections
- Cracking, especially in brittle or high-strength alloys
- Dimensional inaccuracies that affect fit, function, or assembly
To reduce residual stresses and control distortion, several strategies can be employed:
- Pre-weld fixture design: Robust clamping systems resist deformation during the process.
- Symmetric weld paths: Welding in a balanced sequence minimizes cumulative distortion.
- Preheating: Reduces thermal gradients and softens contraction forces.
- Post-weld heat treatment: Relieves residual stress and stabilizes the structure.
- Optimized laser parameters: Slower travel speeds, beam wobbling, or pulse modulation can smooth heat input.
Industry-Specific Joint Design Guidelines
Automotive Lightweight Structures
In automotive manufacturing, laser welding supports the shift toward lighter, stronger vehicles. Components such as body-in-white panels, battery enclosures, and chassis parts use advanced high-strength steels and aluminum alloys. The following is a guide to changing industry connections:
- Favor lap joints for spot replacement and structural joining.
- Minimize flange widths to save weight while maintaining stiffness.
- Ensure a tight fit-up to handle limited gap tolerance in high-speed, automated welding.
- Use hybrid welding for thicker or multi-material joints (e.g., aluminum to steel).
- Incorporate predictive modeling to reduce distortion in large assemblies.
Aerospace Precision Components
Aerospace applications demand extremely high strength-to-weight ratios and strict quality control. Titanium alloys, nickel-based superalloys, and aluminum-lithium alloys are commonly laser welded in thin-walled or hollow structures. The following is a guide to changing industry connections:
- Use butt joints with precise machining for low-profile, full-penetration welds.
- Apply stringent shielding gas control for reactive materials like titanium.
- Design symmetrical weld paths to minimize thermal distortion.
- Validate joints with nondestructive testing (NDT) due to mission-critical safety requirements.
Medical Devices and Implants
Laser welding is ideal for medical applications due to its ability to create clean, narrow, and precisely controlled welds in stainless steel, titanium, and cobalt-chromium alloys. The following is a guide to changing industry connections:
- Use autogenous (filler-free) welds to prevent contamination and minimize foreign material.
- Favor lap and edge joints for small, thin components like surgical tools or stents.
- Ensure smooth weld profiles to eliminate crevices that can harbor bacteria.
- Meet strict documentation and validation standards for biocompatibility.
Electronics and Battery Modules
In consumer electronics and EV batteries, joint design must accommodate thin foils, small terminals, and temperature-sensitive materials like copper, nickel, and polymer coatings. The following is a guide to changing industry connections:
- Use pulsed laser welding for minimal heat input on delicate parts.
- Design lap joints for terminal connections with layered foils.
- Optimize beam focus and spot size for tight tolerance features.
- Avoid spatter and deformation that can damage adjacent sensitive components.
Energy Sector (Fuel Cells, Turbine Components)
Laser welding supports high-efficiency, high-durability systems in energy applications, from hydrogen fuel cells to gas turbine blades. The following is a guide to changing industry connections:
- For fuel cells, use edge or lap welds on thin stainless steel or coated sheets, emphasizing gas-tight, leak-free seals.
- For turbine components, use deep-penetration keyhole welds in nickel-based alloys with controlled cooling to manage residual stress.
- Implement rigorous quality checks for joints exposed to cyclic thermal and pressure loads.
- Use backing gas systems for root protection in full-penetration welds.
Common Failure Modes and Corrective Design Actions
Lack of Fusion or Incomplete Penetration
- Cause: Inadequate laser energy, poor joint fit-up, excessive gap, or misalignment.
- Corrective Actions:
- Optimize laser parameters (power, speed, focus).
- Tighten tolerances on joint gap and edge prep.
- Redesign joint geometry to better expose fusion faces (e.g., transition lap to butt joint).
- Improve fixturing to maintain alignment during welding.
Porosity and Gas Entrapment
- Cause: Entrapped gases due to surface contaminants, improper shielding gas, or unstable keyhole behavior.
- Corrective Actions:
- Clean materials thoroughly before welding.
- Optimize shielding gas flow and composition (e.g., use argon-helium mix).
- Adjust the laser power and speed to stabilize the keyhole mode.
- Consider beam oscillation to allow gases to escape during solidification.
Cracking (Hot Cracking, Solidification Cracking)
- Cause: Rapid cooling, high shrinkage stress, or brittle intermetallic compounds—especially in dissimilar metal joints or certain aluminum alloys.
- Corrective Actions:
- Modify alloy selection or use compatible filler metals (if allowed).
- Preheat the base material to reduce thermal gradients.
- Use joint designs that reduce constraints, such as tapered or scarfed edges.
- Apply post-weld heat treatment if necessary.
Undercut and Overfill
- Cause: Excessive laser energy, improper beam angle, or poor alignment.
- Corrective Actions:
- Re-calibrate the beam position relative to the joint.
- Adjust power and travel speed to match material thickness.
- Use wobble welding or beam shaping to smooth the weld profile.
Distortion and Warping
- Cause: Uneven heat input, insufficient clamping, or asymmetric joint design.
- Corrective Actions:
- Use symmetric weld patterns to balance heat distribution.
- Improve fixturing and restraint methods.
- Consider staggered weld sequences in large or thin parts.
- Run thermal simulations to predict distortion and adjust the design accordingly.
Fatigue Failure
- Cause: Stress concentrations at the weld toe or poor surface finish; cyclic loading exacerbates the issue.
- Corrective Actions:
- Design joints to reduce abrupt geometry changes (e.g., add radius transitions).
- Minimize notch effects by optimizing weld bead shape (flat to slightly convex).
- Use post-weld surface finishing or laser peening to improve fatigue resistance.