Introduction
Available Models
-
Double Wobble Pulse Laser Cleaning Machine
Rated 4.75 out of 5$4,300 – $16,000 This product has multiple variants. The options may be chosen on the product page -
Luggage Pulse Laser Cleaning Machine
Rated 5.00 out of 5$6,300 – $16,800 This product has multiple variants. The options may be chosen on the product page -
Backpack Pulse Laser Cleaning Machine
Rated 4.75 out of 5$6,600 – $8,900 This product has multiple variants. The options may be chosen on the product page
Application
The 100w pulse laser cleaning machine is an efficient and versatile tool designed for a wide range of cleaning applications across various industries. Its precision and adaptability make it ideal for tasks that require gentle yet effective surface treatment. Common applications include:
- Rust Removal: Easily eliminates rust from metal surfaces without damaging the underlying material.
- Paint Stripping: Effectively removes paint and coatings from surfaces, preparing them for refinishing or repair.
- Oil and Grease Cleaning: Cleans machinery, tools, and equipment by removing stubborn oil, grease, and other residues.
- Mold and Oxide Removal: Removes oxides and molds from components to improve performance and aesthetics.
- Surface Preparation: Prepares surfaces for welding, bonding, or coating by cleaning and smoothing.

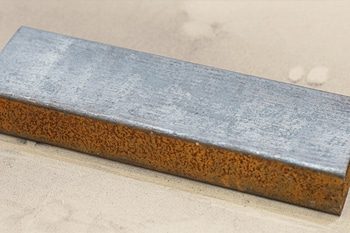
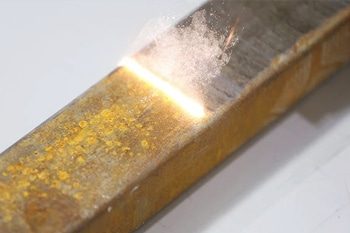
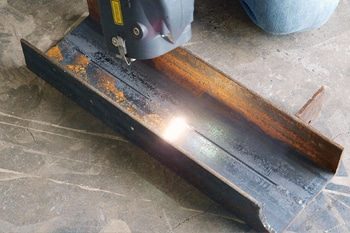

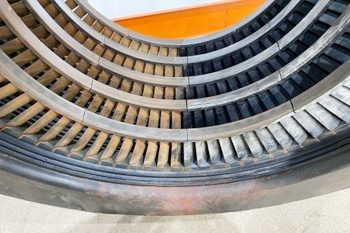
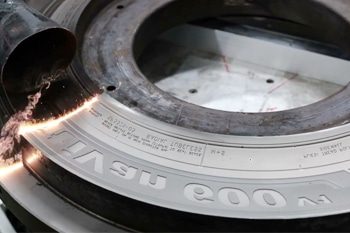
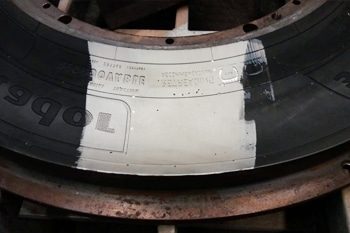
Comparison with Traditional Cleaning Methods
Aspect | Laser Cleaning | Sandblasting | Chemical Cleaning | Ultrasonic Cleaning |
Contact with Surface | Non-contact, no physical abrasion | Contact-based, abrasive material impacts the surface | Non-contact, but chemicals may react with the surface | Non-contact, but uses cavitation bubbles in a liquid medium |
Environmental Impact | Eco-friendly, no chemicals or solvents used | Generates dust and airborne particles, which can be harmful | Often uses toxic chemicals, generates hazardous waste | Requires disposal of used cleaning fluids |
Precision and Control | High precision, selective cleaning of specific areas | Less precise, may erode the surface or surrounding material | Limited precision, can affect the entire surface | High precision but limited to small, submerged parts |
Surface Integrity | Preserves surface integrity, ideal for sensitive materials | Can damage or roughen the surface, especially on delicate materials | Can cause chemical reactions that may alter surface properties | Generally preserves surface but not suitable for all materials |
Residue and Waste | Minimal residue, no secondary waste | Leaves abrasive particles as waste | Leaves chemical residues, produces secondary waste | Leaves contaminants in the cleaning solution |
Maintenance and Downtime | Low maintenance, minimal downtime | Requires regular replenishment of abrasive material and equipment wear | Frequent chemical replacement and safety measures needed | Requires regular maintenance of ultrasonic equipment |
Safety | Safer for workers, no harmful chemicals or particles | Risk of inhalation and physical harm from abrasive particles | Risk of chemical burns, inhalation, and environmental contamination | Safer, but risks associated with handling and disposing of cleaning fluids |
Versatility | Suitable for a wide range of materials and industries | Primarily used for robust materials, not ideal for delicate surfaces | Versatile, but limited by chemical compatibility with materials | Limited to small parts that can be submerged in the cleaning tank |
Cost-Effectiveness | Higher initial cost but cost-effective in the long term | Lower initial cost but higher ongoing expenses due to abrasive consumption | Low initial cost but high cost for chemicals and disposal | Moderate cost, but limited to specific applications |
Operational Speed | Fast and efficient, reduces overall cleaning time | Can be slow, especially on large or intricate surfaces | Varies depending on chemical reaction time and safety protocols | Fast for small items, but limited by the size of the ultrasonic tank |
Why Choose Us
Cutting-Edge Technology
Maxcool CNC is committed to integrating the latest technological advancements into our machines. Our laser cleaning machines feature precise control, high efficiency, and superior performance, ensuring optimal cleaning results for various industrial applications.
Reliable and Durable Equipment
Our machines are built to last, with robust construction and high-quality components that guarantee long-term reliability and minimal maintenance. You can trust Maxcool CNC to provide equipment that withstands even the toughest environments.
Comprehensive Support
From pre-sales consultation to after-sales technical assistance, we are with you every step of the way. Our dedicated support team ensures you have all the information and help you need to maximize the value of your investment.
Sustainability and Efficiency
Maxcool CNC’s laser cleaning machines are designed with energy efficiency in mind, reducing power consumption without compromising performance. This not only lowers operational costs but also contributes to a more sustainable future.
Customer Reviews
Frequently Asked Questions
How Does a Pulse Laser Cleaning Machine Work?
Is the Machine Safe to Use?
Does it Damage the Base Material?
Does it Require Training to Operate?
What Are the Limitations of This Machine?
What is the Accuracy of Cleaning?
Related Resources
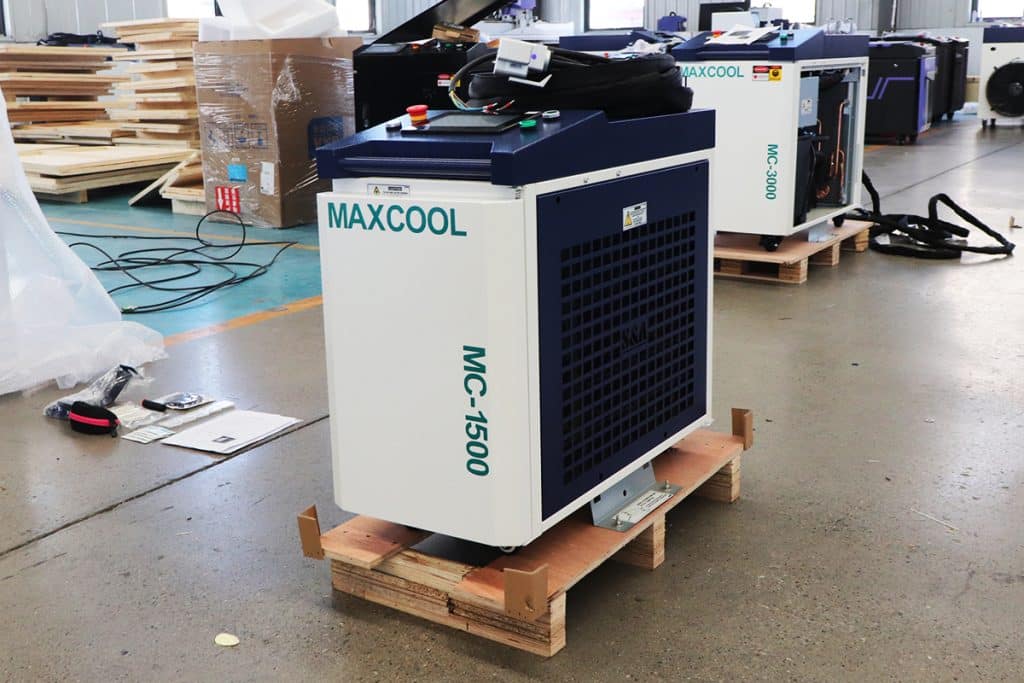
What Are The Applications of Laser Cleaning Machines?
This article explores the various industrial and specialized applications of laser cleaning machines, detailing how the technology is used across multiple sectors and processes.
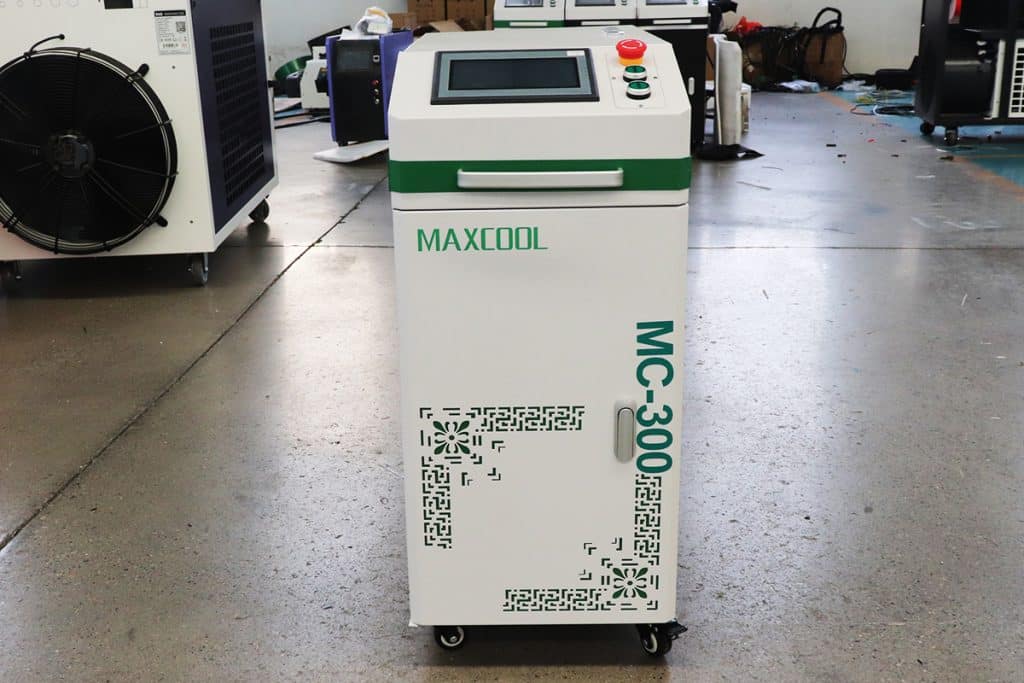
Does Pulsed Laser Cleaning Damage The Substrate?
Explores pulsed-laser cleaning fundamentals, potential substrate damage, controlling parameters, industry case studies, and best practices for safe, efficient surface treatment.
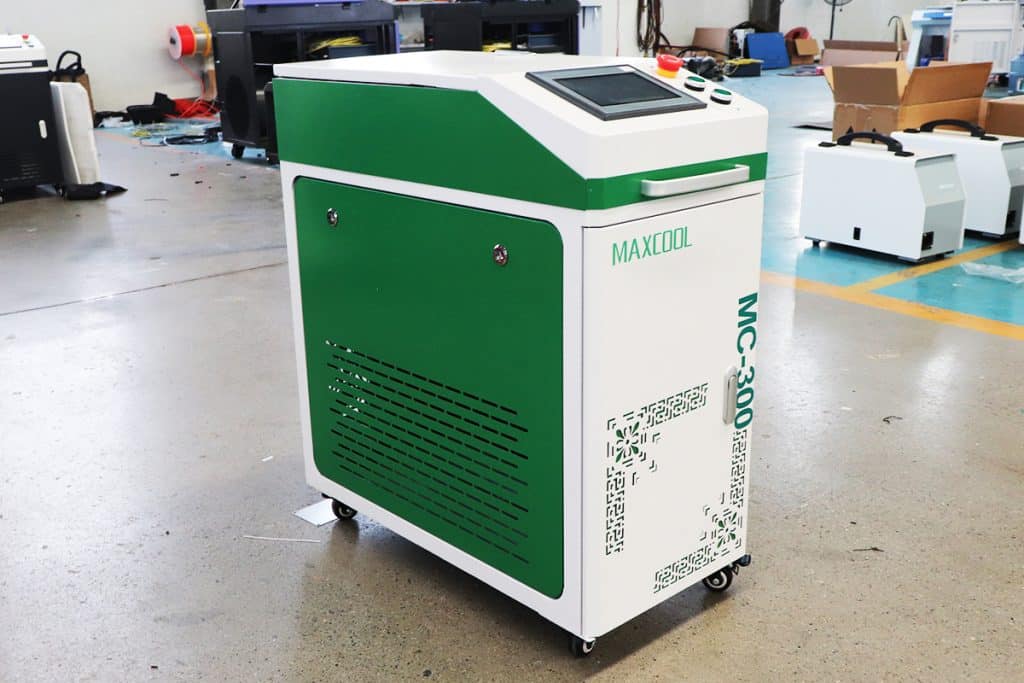
Does Laser Cleaning Affect Lifespan and Durability of The Surface Being Cleaned?
This article explores how laser cleaning interacts with different materials and examines its effects on surface lifespan, durability, and structural integrity.