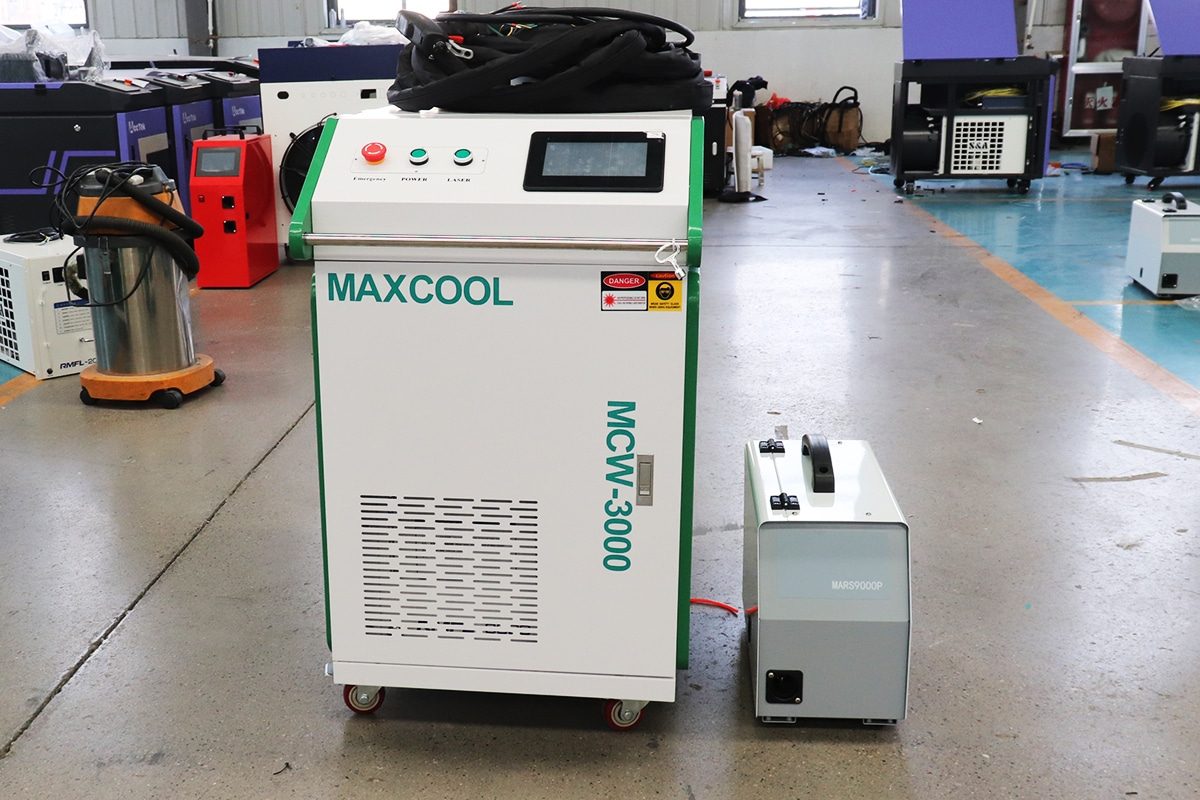
The Role of Thermal Management in Laser Cleaning
Cooling System Architectures in Modern Machines
Cooling systems in laser cleaning machines typically fall into two main categories: air-cooled and liquid-cooled architectures.
- Air-Cooled Systems: These are commonly found in low- to mid-power laser units (under 1000W). Air-cooled systems rely on internal fans and strategically placed heat sinks to draw heat away from critical components. Some designs integrate forced-air flow channels or high-efficiency fin structures to improve heat dissipation. While simpler and lower-cost, these systems are more sensitive to ambient temperatures and are less effective in high-duty-cycle applications.
- Liquid-Cooled Systems: Found in high-power or industrial-grade laser cleaning machines, liquid-cooled systems use water or a coolant mixture to absorb and carry away heat. The architecture includes a reservoir, pump, heat exchanger (or radiator), tubing, and temperature sensors. These systems offer superior heat transfer, better temperature stability, and longer continuous operation times. They also often include smart features like real-time temperature monitoring, coolant flow sensors, and automatic shutoff mechanisms in case of failure.
Core Components and Their Functions
Reservoir and Expansion Tank
Maintenance Tips:
- Check the coolant level regularly.
- Inspect for leaks or cracks.
- Ensure the cap seals properly to maintain pressure.
Pump
Maintenance Tips:
- Listen for unusual noises (grinding or cavitation).
- Check for vibration or irregular operation.
- Inspect seals and connectors for leaks.
Heat Exchanger (Radiator or Chiller)
Maintenance Tips:
- Clean fins or coils to prevent clogging.
- Monitor for scaling or corrosion.
- Ensure fans or condenser units operate properly.
Filters and Strainers
Maintenance Tips:
- Clean or replace filters as part of routine service.
- Use a proper mesh size for your application.
- Inspect for buildup that may restrict flow.
Temperature, Flow, and Pressure Sensors
Maintenance Tips:
- Calibrate sensors periodically.
- Check sensor readings against actual conditions.
- Replace faulty sensors promptly to avoid damage.
Hoses, Fittings, and Quick Disconnects
Maintenance Tips:
- Inspect hoses for cracks, kinks, or swelling.
- Tighten or replace loose fittings.
- Clean quick disconnects to prevent contamination.
Failure Modes and Early-Warning Signs
Progressive Fouling and Scaling
Early-Warning Signs:
- Reduced coolant flow rate
- Rising outlet temperatures
- Visible scaling in transparent hoses or tanks
- Alarms for temperature threshold exceedance
Micro-Leaks
Early-Warning Signs:
- Unexplained coolant loss over time
- Air bubbles are visible in the coolant lines
- Moisture or staining around joints and seals
- Drop in system pressure
Pump Cavitation
Early-Warning Signs:
- Loud rattling or grinding noises
- Irregular coolant flow
- Sudden drops in pressure or flow rate
- Vibration around the pump housing
Fan or Compressor Wear
Early-Warning Signs:
- Excessive fan noise or rattling
- Poor heat dissipation despite adequate coolant levels
- Irregular fan speeds or stalling
- Overheating during normal load
Sensor Drift
Early-Warning Signs:
- Inconsistent readings compared to manual gauges
- Alarms are triggering without visible problems
- Lack of alarms despite rising temperature
- Frequent false fault codes
Increased Electrical Consumption
Early-Warning Signs:
- Rising energy usage despite unchanged workloads
- Overheating of electrical enclosures
- Unexpected circuit breaker trips
- Heat exchanger or chiller working longer than normal cycles
Laser Power Derate
Early-Warning Signs:
- Sudden drop in cleaning performance
- Software notifications or logs showing power derating
- The machine fails to reach the target output despite full settings
- Repeated thermal shutdowns
Designing a Preventive Maintenance Schedule
Daily (Shift-Based) Checks
These are frontline inspections performed at the beginning or end of each shift. They take only a few minutes but are critical for spotting immediate risks.
- Check coolant levels in the reservoir and expansion tank.
- Look for leaks around hoses, fittings, and pump seals.
- Confirm the system is operating within normal temperature and pressure ranges.
- Visually inspect for bubbles, blockages, or abnormal flow in coolant lines.
- Listen for unusual noises from pumps or fans.
Weekly Routines
Weekly checks go deeper than daily inspections, focusing on components that show wear over a few days of use.
- Clean air filters or external vents on radiators or chillers.
- Inspect hoses for surface cracks, kinks, or bulging.
- Verify sensor readings (temperature, pressure, flow) for consistency.
- Drain and flush the system if signs of contamination or fouling are noticed.
- Check the pump and fan function under load.
Monthly and Quarterly Tasks
These tasks address system performance and component degradation that accumulates over time.
- Test and recalibrate sensors to ensure accurate readings.
- Inspect and clean heat exchangers, coils, or radiators to remove dust and mineral buildup.
- Replace inline filters and strainers.
- Review system logs for abnormal trends in temperature, flow, or energy consumption.
- Perform a thermal performance test under full load to assess efficiency.
Annual Overhauls
Once a year (or more frequently in high-demand environments), a full inspection and refurbishment should be scheduled to reset the system’s baseline.
- Drain and replace the entire coolant supply with fresh, manufacturer-recommended fluid.
- Replace worn-out hoses, fittings, and seals.
- Deep-clean or descale the heat exchanger and pump interior.
- Test the pressure-relief system and safety interlocks.
- Update firmware or software for sensors and control units, if applicable.
- Document all actions and update the maintenance log.
Daily and Weekly Tasks
Every Start-Up
Before powering up the machine, verify that the cooling system is ready for operation.
- Check the coolant level in the reservoir and expansion tank; top off with manufacturer-approved coolant if needed.
- Inspect hoses, quick-disconnects, and fittings for visible leaks, cracks, or bulges.
- Examine the system for air bubbles in transparent coolant lines or the expansion tank (a sign of possible micro-leaks or pump issues).
- Ensure fans or chiller units are free from obstructions and can spin freely.
- Review control panel indicators for any fault lights or abnormal temperature/pressure readings before operation begins.
End of Shift
After each use, a brief inspection can help detect wear or damage caused during operation.
- Inspect coolant color and clarity for signs of contamination (cloudiness, debris, or discoloration).
- Listen for irregular sounds from pumps or fans that may suggest cavitation or bearing wear.
- Check the temperature logs or system readouts to see if any parameters approached warning or limit values.
- Look for drips or pooled fluid beneath the machine, especially near joints and seals.
- Wipe down exterior components to remove dust buildup from fans or vents.
Weekly Maintenance Tasks
At least once per week, perform a more in-depth check of key cooling system components.
- Clean air filters and vent grills to maintain strong airflow in air-cooled or hybrid systems.
- Inspect the radiator or heat exchanger fins for dust, lint, or oil buildup that could reduce heat transfer.
- Verify sensor readings for temperature, flow, and pressure against expected values.
- Test pump and fan operation under load, ensuring consistent performance without noise or overheating.
- Review coolant inventory and logs, ensuring fluid type, concentration, and pH are within spec (especially in hard water regions).
- Record all checks and findings in a maintenance log to track system health over time.
Monthly and Quarterly Tasks
Monthly Maintenance Tasks
- Sensor Accuracy Check
- Verify temperature, pressure, and flow sensor readings against manual gauges or reference devices.
- Recalibrate sensors if readings are inconsistent or deviate from expected norms.
- Coolant Inspection and Basic Testing
- Test the coolant’s concentration, pH, and conductivity using appropriate test strips or digital meters.
- Look for signs of degradation: cloudiness, odor, discoloration, or sludge.
- Top off with fresh coolant or replace partially if the chemical balance is off.
- Visual Inspection of Internal Components
- Open accessible panels to inspect internal cooling lines and fittings for hidden leaks or corrosion.
- Check clamps, seals, and gaskets for early signs of fatigue.
- Chiller or Radiator Performance Review
- Measure the inlet and outlet temperature differential to assess heat exchanger efficiency.
- Clean radiator fins or chiller coils if airflow is reduced or fouling is visible.
Quarterly Maintenance Tasks
- Filter and Strainer Replacement
- Replace all inline filters and strainers that capture particles and debris in the cooling circuit.
- Flush the system if filters appear heavily loaded or fluid shows contamination.
- Pump and Fan Condition Assessment
- Test pump pressure and flow rate under load; replace worn impellers or seals if needed.
- Inspect and lubricate fan bearings if applicable.
- Listen for excessive noise that may indicate mechanical wear.
- Heat Exchanger Deep Clean
- Use non-corrosive cleaning agents or flushing tools to remove scaling, mineral buildup, or oil residue.
- For closed-loop chillers, inspect internal refrigerant pressure and performance.
- System Performance Logging and Analysis
- Export and review performance logs (if available) to identify trends like rising temperature baselines, increased power consumption, or derating events.
- Adjust setpoints or controls based on trends to optimize cooling system response.
Annual Overhaul and Life-Cycle Considerations
Annual Overhaul Tasks
- Coolant System Flush and Replacement
- Drain the entire system, including reservoir, hoses, heat exchanger, and pump housing.
- Flush with manufacturer-approved cleaning agents to remove scaling, biofilm, and sediment.
- Refill with fresh coolant at the correct concentration and pH, ideally using pre-mixed or deionized water-based solutions to avoid mineral contamination.
- Hose and Seal Replacement
- Replace all rubber hoses, quick-disconnects, O-rings, and gaskets—even if no leaks are visible.
- Over time, these materials degrade due to temperature cycling and exposure to coolant chemicals, risking sudden failure.
- Sensor Calibration and Software Updates
- Recalibrate all temperature, flow, and pressure sensors using certified references.
- Check for and apply firmware or software updates for control systems that manage thermal behavior.
- Pump and Fan Rebuild or Replacement
- Inspect internal pump components (impeller, shaft seals, bearings) for wear or erosion.
- Replace if the flow rate or pressure has dropped significantly.
- For fan or compressor units, clean or replace worn motors and check for bearing play or imbalance.
- Heat Exchanger Deep Maintenance
- Perform chemical descaling of internal surfaces (if compatible), or use ultrasonic cleaning where applicable.
- Inspect metal surfaces for corrosion or pitting that could lead to leaks or thermal inefficiency.
- System Pressure Testing and Leak Check
- Pressurize the cooling loop and monitor for pressure loss to detect hidden micro-leaks.
- Use UV dye or electronic leak detectors for non-obvious failures.
Life-Cycle Considerations
Beyond routine service, the annual overhaul is the time to take stock of the cooling system’s aging components and their future viability:
- Component Life Expectancy: Most pumps, fans, and sensors have a service life of 2–5 years under regular use. Tracking usage hours helps plan replacements before failures occur.
- Performance Trends: Compare current operating parameters (flow rate, heat rejection, energy use) to baseline data. A consistent decline may signal deeper system fatigue.
- Upgrade Potential: Evaluate newer components (e.g., more efficient chillers, smart sensors) that could reduce energy costs or improve reliability. Retrofit kits may be available for older machines.
- Budget Planning: Include anticipated component replacements in your maintenance budget to avoid surprise costs during the next operating year.
Detailed Procedures for Key Tasks
Coolant Replacement
Procedure:
- Power down the machine and allow it to cool completely.
- Drain the existing coolant from the reservoir and all accessible lines. Use appropriate containers to avoid spills.
- Flush the system with a compatible cleaning solution or deionized water to remove residue, scale, and biofilms. Run the flush through the entire loop if possible.
- Inspect hoses and fittings for any wear, leaks, or blockages while the system is empty.
- Refill the reservoir with new coolant—use the manufacturer-recommended type and concentration (usually glycol-based or deionized water with corrosion inhibitors).
- Bleed air from the system, using bleed valves or by running the pump briefly with the reservoir cap off, to remove trapped air bubbles.
- Check for leaks, restore system pressure, and monitor temperature and flow upon restart.
Filter Change
Procedure:
- Locate the inline filters or strainers—usually near the reservoir, pump inlet, or return lines.
- Shut off and depressurize the system to avoid fluid spray or backflow.
- Remove the filter housing and carefully extract the old filter element.
- Inspect the filter for debris, corrosion, or foreign material. Note any unusual buildup (it may indicate larger system issues).
- Clean the housing thoroughly before inserting the new filter.
- Install the replacement using proper orientation and ensure a tight seal to prevent leaks.
- Restart the system, monitor for pressure drops, and verify that flow returns to normal.
Heat-Exchanger Cleaning
- Procedure (Air-Cooled Systems):
- Turn off the power to the fans and cooling system.
- Vacuum or blow out dust from radiator fins using compressed air (blow from the inside out for best results).
- Use a soft brush or fin comb to remove stubborn debris without damaging the fins.
- Wipe down fan blades and motor housings.
- Procedure (Liquid-Cooled Systems):
- Flush the system with a descaling solution compatible with copper, stainless steel, or aluminum, depending on your heat exchanger material.
- Circulate the cleaning fluid for the recommended time (typically 30–60 minutes).
- Drain and rinse the system with clean water or neutralizing solution.
- Refill with fresh coolant and check for pressure and flow consistency.
Troubleshooting Guide
High-Temperature Alarm
- Symptoms: The system triggers a high-temp warning, derates laser power, or shuts down to prevent overheating.
- Possible Causes:
- Fouled or clogged heat exchanger
- Insufficient coolant level
- Pump malfunction or cavitation
- Fan or chiller failure
- The ambient temperature is too high
- Troubleshooting Steps:
- Check and top off the coolant level in the reservoir.
- Inspect the radiator or chiller for dirt, dust, or blocked airflow.
- Listen for pump noise; if cavitating, inspect for air bubbles or low inlet pressure.
- Confirm fans or compressors are running at normal speed.
- Ensure the machine is operating in a temperature-controlled environment.
Low-Flow Alarm
- Symptoms: Alarm indicating coolant flow rate is below safe limits.
- Possible Causes:
- Clogged filters or strainers
- Blockage or kinks in hoses
- Pump wear or failure
- Air in the coolant loop
- Coolant viscosity too high (e.g., due to cold startup or contamination)
- Troubleshooting Steps:
- Replace or clean filters and strainers.
- Inspect hoses for crimps, bends, or obstructions.
- Check the pump for reduced output, strange noises, or overheating.
- Bleed the system to remove trapped air.
- Warm coolant to operating temperature or replace if thickened or dirty.
Compressor Fault (Chiller-Based Systems)
- Symptoms: Chiller fails to maintain coolant temperature; fault code displayed; system shuts down or cycles repeatedly.
- Possible Causes:
- Refrigerant leak or low refrigerant pressure
- Compressor overheating due to dirty coils or blocked airflow
- An electrical fault in the motor or the capacitor
- Faulty pressure sensor
- Troubleshooting Steps:
- Inspect chiller coils for dust and debris; clean thoroughly.
- Check fan operation and verify ambient airflow is sufficient.
- Review compressor run cycles—rapid cycling may indicate sensor failure or refrigerant issues.
- If equipped, read refrigerant pressure and temperature logs.
- Call qualified HVAC or chiller service if refrigerant handling is required.
Unstable Coolant Conductivity
- Symptoms: Alarms or system logs showing erratic conductivity readings; may trigger derating or shutoff.
- Possible Causes:
- Contaminated coolant (metal ions, biological growth)
- Mixing of incompatible coolant types
- Sensor drift or failure
- Leaching from degraded hoses or fittings
- Troubleshooting Steps:
- Test the coolant with a handheld conductivity meter.
- Drain and flush the system; refill with fresh, approved coolant.
- Avoid mixing brands or types of coolant without compatibility confirmation.
- Calibrate or replace conductivity sensors.
- Replace aging hoses or plastic components that may be breaking down chemically.