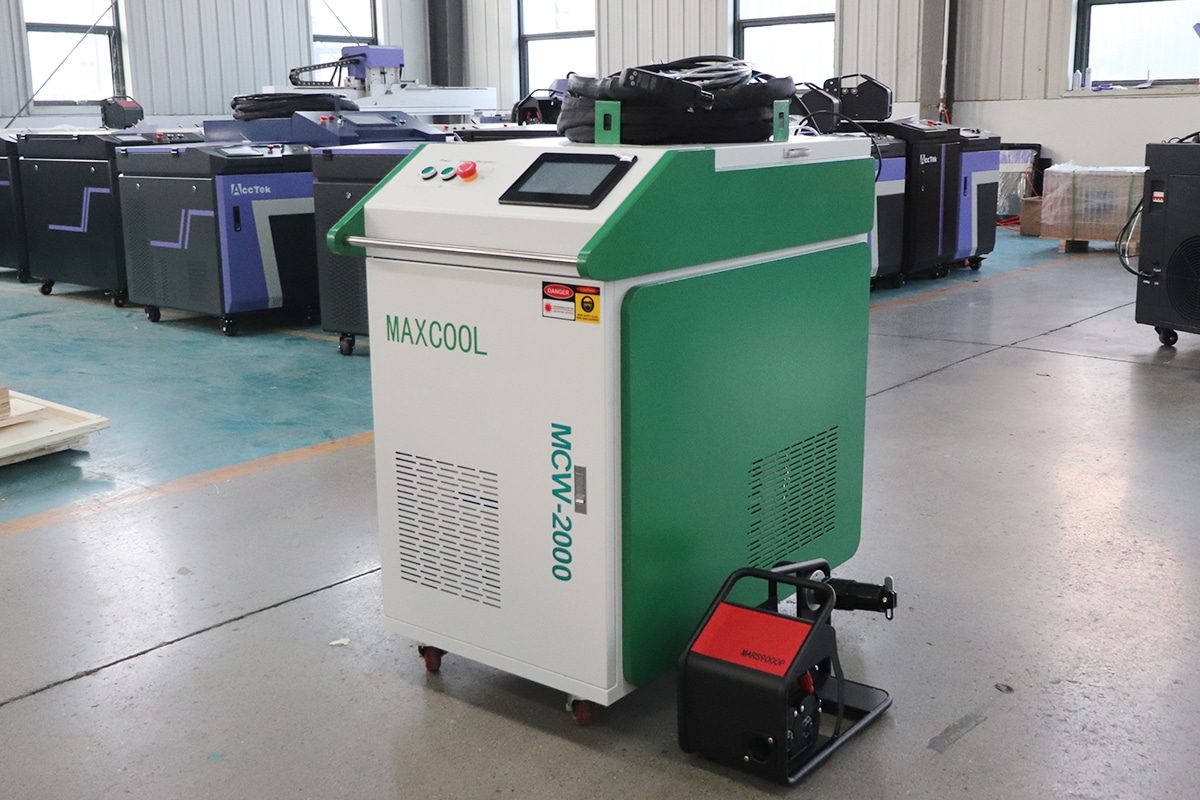
Understanding Pulsed Laser Cleaning
Photothermal Ablation
Photomechanical Ablation
Photochemical Ablation
Critical Parameters in Pulsed Laser Cleaning
Pulse Duration
Pulse Energy
Repetition Rate
Laser Wavelength
Laser wavelength influences how energy is absorbed by different materials. Materials have unique absorption spectra, so choosing the appropriate wavelength is critical for selective cleaning. For example:
- 1064 nm (infrared, Nd:YAG) is effective for removing rust, oxides, and metallic contaminants.
- 532 nm (green, frequency-doubled Nd:YAG) provides better contrast between many coatings and metal surfaces.
- 355 nm or 266 nm (ultraviolet) allows for photochemical ablation and is ideal for organic residues or thin films on sensitive substrates.
Beam Profile
Factors Affecting the Quality of Pulsed Laser Cleaning
Material Properties
The substrate material plays a major role in how it responds to laser energy. Three key properties affect cleaning performance:
- Thermal Conductivity: Materials with high thermal conductivity (e.g., copper, aluminum) dissipate heat quickly, which can reduce localized temperature rise and minimize damage. However, this can also reduce the efficiency of thermal-based ablation. Low-conductivity materials (e.g., ceramics) retain heat longer, increasing cleaning efficiency but raising the risk of overheating.
- Absorption Coefficient: This measures how effectively a material or contaminant absorbs laser energy at a given wavelength. A higher absorption coefficient leads to more efficient energy conversion and better cleaning. Matching the laser wavelength to the peak absorption of the contaminant (not the substrate) ensures more selective removal.
- Reflectivity: Highly reflective materials (e.g., polished metals) can reflect a large portion of the laser energy, reducing effectiveness and requiring higher energy input. Surface roughness, oxidation, or pre-treatment can help reduce reflectivity and improve energy absorption.
Environmental Conditions
Ambient conditions during laser cleaning can influence energy transfer and material behavior. Two important environmental factors include:
- Ambient Temperature: Higher temperatures can reduce the energy needed to initiate ablation by preheating the material, but excessive heat may affect the substrate or nearby components. Low temperatures might make some contaminants more brittle and easier to remove, but can reduce overall ablation efficiency.
- Humidity: Moisture in the air can interact with the laser beam and the surface, especially during high-energy pulses. In some cases, humidity helps by forming micro-plasma or aiding in contaminant breakdown. However, excessive humidity may cause condensation or oxidation, which could hinder cleaning or introduce new surface layers.
Contaminant Properties
The type, thickness, and adhesion strength of the contaminant layer are major factors in determining cleaning success:
- Composition: Organic residues, oxides, paints, and carbon deposits each respond differently to laser energy. For example, organic contaminants may decompose chemically under UV light, while oxides may require thermal or mechanical ablation.
- Thickness: Thicker layers typically require more energy or multiple passes to remove completely. Layer uniformity also impacts how evenly the laser can clean the surface.
- Adhesion Strength: Contaminants that are loosely bonded to the substrate are easier to remove via photomechanical or photothermal effects. Strongly bonded layers may need higher pulse energy or optimized pulse durations to break the bond without damaging the base material.
Strategies to Improve the Quality of Pulsed Laser Cleaning
Optimal Parameter Selection
Fine-tuning the core laser parameters is critical for effective and selective cleaning. Each parameter must be adapted to the material, contaminant type, and cleaning objective:
- Pulse Duration: Use shorter pulses (picoseconds or femtoseconds) for delicate or heat-sensitive surfaces to minimize thermal diffusion. Longer pulses (nanoseconds) are suitable for more robust contaminants or thicker layers.
- Pulse Energy: Set the energy just above the ablation threshold of the contaminant but below that of the substrate. This avoids surface damage while ensuring complete removal.
- Repetition Rate: Balance cleaning speed and heat management. Higher repetition rates increase throughput but may cause heat buildup. Adjust based on material thermal properties.
- Wavelength Selection: Choose a wavelength that matches the absorption peak of the contaminant. For example, UV lasers are effective for organic and thin film removal, while infrared lasers work well on rust and oxides.
- Beam Profile Optimization: A uniform (top-hat) beam profile provides even energy distribution, resulting in more consistent cleaning than a Gaussian profile, which can cause uneven results and localized overheating.
Advanced Monitoring and Control Systems
Implementing intelligent systems improves reliability and process control:
- Real-Time Monitoring: Use sensors (e.g., cameras, spectrometers, thermal detectors) to track surface temperature, reflectivity, or plume formation during cleaning. This allows operators to identify when a surface is clean or if parameters need adjustment.
- Feedback Control: Integrate monitoring data into an automated feedback loop to dynamically adjust pulse energy, scanning speed, or repetition rate in real time. Adaptive systems help maintain quality even when material conditions vary.
Pre-Cleaning Surface Preparation
Preparing the surface before laser cleaning can enhance efficiency and reduce the energy required for effective removal:
- Mechanical Pre-Cleaning: Light brushing, air blasting, or ultrasonic cleaning can dislodge loose particles and reduce contaminant thickness, making the laser process more focused and efficient.
- Chemical Pre-Treatment: Applying suitable solvents or mild acids can weaken the bond between the contaminant and substrate. This is particularly useful for stubborn residues or layered deposits that are difficult to remove with laser energy alone.
Challenges and Solutions
Managing Thermal Effects
- Challenge: Excessive heat buildup can damage the substrate, especially when using higher pulse energies or repetition rates. Thermal effects can cause discoloration, micro-cracks, or material deformation, particularly on sensitive surfaces.
- Solution: Use shorter pulse durations (picoseconds or femtoseconds) to localize energy delivery and minimize heat diffusion. Optimize repetition rate and scanning speed to allow time for heat dissipation. Implementing cooling systems or inert gas flows can also help manage temperature rise during cleaning.
Addressing Material Variability
- Challenge: Different materials—and even different regions of the same surface—can have varying thermal conductivity, reflectivity, or absorption characteristics. This variability can lead to uneven cleaning or surface damage if not accounted for.
- Solution: Conduct preliminary testing on representative material samples to identify ideal laser parameters. Use adjustable systems with multiple wavelength options or variable pulse settings to adapt to different materials. Incorporate real-time monitoring tools that detect surface conditions and enable dynamic parameter adjustment.
Ensuring Consistency
- Challenge: Maintaining consistent cleaning quality across large areas or in automated production lines can be difficult. Factors such as beam misalignment, contaminant thickness, or equipment drift can degrade results over time.
- Solution: Implement real-time process monitoring with feedback control to maintain stable operation. Use automated scanning systems with precise beam positioning and overlap control to ensure uniform coverage. Regular system calibration and maintenance are also essential for consistent performance.