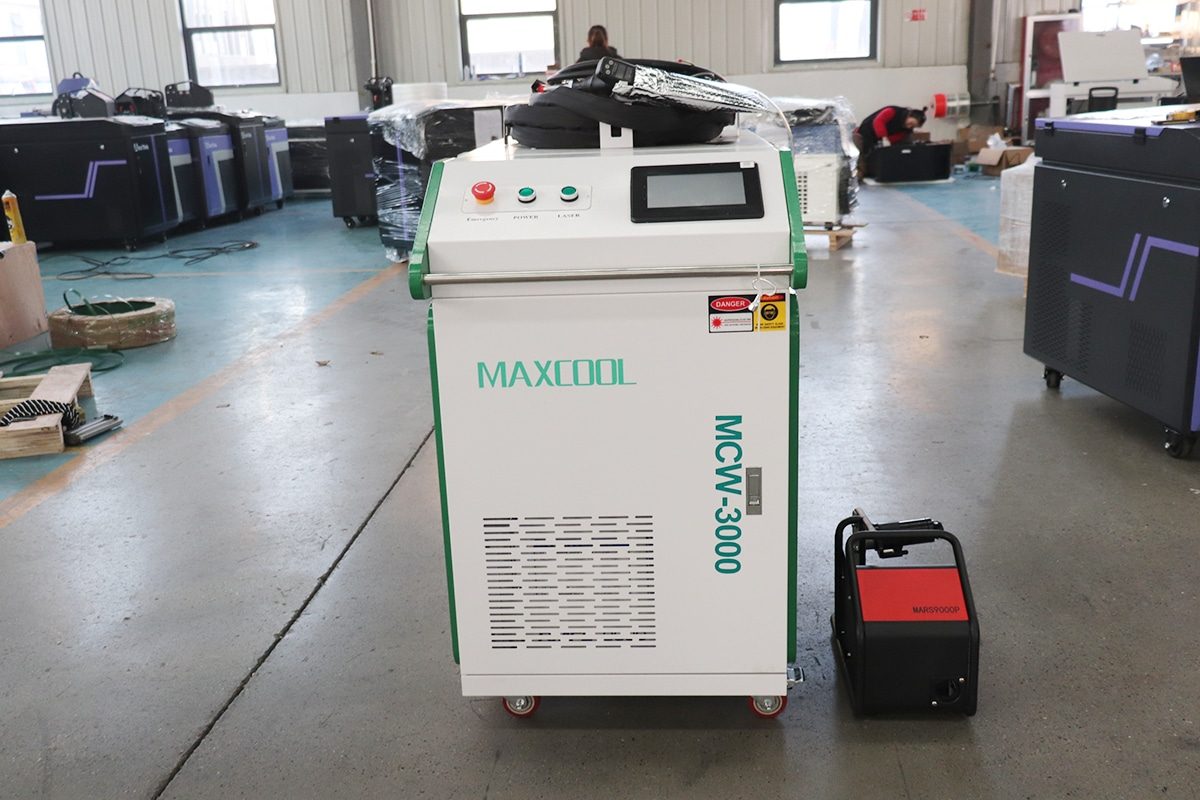
How To Improve The Quality Of Continuous Laser Cleaning?
Continuous laser cleaning has become a critical process in industries requiring precise, non-contact surface preparation and contaminant removal. Unlike pulsed systems, continuous laser cleaning machines operate with a steady laser beam, offering advantages such as consistent energy delivery, faster cleaning speeds, and improved integration with automated production lines. These machines are widely used for removing rust, paint, oxides, oils, and other residues from metals and complex surfaces in sectors like automotive, aerospace, and heavy manufacturing.
However, achieving high-quality results with continuous laser cleaning is not automatic. The process is influenced by multiple variables, including laser power, beam focus, scanning speed, and material properties. Without careful optimization, outcomes can range from inefficient cleaning to surface damage or inconsistent results. As the demand for precision and productivity grows, manufacturers and technicians need to understand how to fine-tune their laser cleaning setups for maximum efficiency and surface quality.
This article explores practical strategies to improve the quality of continuous laser cleaning, from equipment settings and maintenance to environmental controls and process monitoring. Whether you’re implementing the technology for the first time or looking to upgrade an existing system, these insights will help ensure you get cleaner, safer, and more reliable results.
Table of Contents
Understanding Laser Cleaning
Laser cleaning is a surface treatment process that uses focused laser energy to remove unwanted materials, such as rust, paint, oil, or oxides, from a substrate. It works by delivering high-energy laser beams that vaporize or ablate contaminants without damaging the underlying material. In continuous laser cleaning, the laser operates in a steady, uninterrupted mode, offering consistent energy output ideal for high-speed and large-area applications.
The core advantage of laser cleaning over traditional methods (like sandblasting or chemical cleaning) is its precision, repeatability, and minimal environmental impact. There’s no need for abrasives or solvents, and waste is limited to the removed material. Continuous lasers, in particular, excel in production environments where speed and consistency are critical.
The process depends on several interacting variables. These include laser wavelength, beam intensity, focal length, and the speed at which the laser is moved across the surface. The surface condition of the target material—its texture, reflectivity, and contamination type—also plays a significant role.
Understanding how continuous laser cleaning works at a fundamental level is the first step to improving its quality. By recognizing the mechanisms at play and how each parameter influences the outcome, operators can begin to control the process more effectively and achieve better, more uniform results.
Selecting Appropriate Laser Parameters
To improve the quality of continuous laser cleaning, one of the most critical steps is fine-tuning the laser parameters. These directly influence how effectively the laser removes contaminants and how safely it interacts with the base material. The three most important parameters to control are laser power, beam spot size, and scanning speed. Each of these settings affects cleaning quality, speed, and the risk of surface damage.
Laser Power
Laser power determines the total amount of energy delivered per second. Higher power levels are effective for removing thick layers of rust, scale, or paint in a single pass, making them ideal for heavy-duty cleaning. However, too much power can lead to overheating, substrate melting, or discoloration, especially on sensitive materials like aluminum or thin metal sheets. On the other hand, using too little power may result in incomplete cleaning and reduced productivity. The key is to match power output with the type and thickness of the contaminant while considering the heat tolerance of the substrate. Power typically ranges between 1 kW and 6 kW in industrial setups, and testing is often required to find the ideal point.
Beam Spot Size
The beam spot size affects how concentrated the laser energy is on the surface. A smaller spot size increases energy density (power per unit area), which enhances the ability to remove tightly bonded or resistant contaminants. It’s well-suited for detailed work or surfaces with complex geometries. However, smaller spots mean slower coverage and may require multiple passes for larger areas. Larger spot sizes, by contrast, allow faster cleaning over broader surfaces but reduce energy intensity, which may be insufficient for tough deposits. Adjustable optics or interchangeable lenses are often used to modify spot size depending on the application.
Scanning Speed
Scanning speed is the rate at which the laser beam moves across the surface, usually measured in mm/s or m/min. It controls how long the laser energy interacts with each point on the material. Slower speeds increase exposure time, boosting cleaning effectiveness but also raising the risk of heat accumulation and substrate damage. Faster speeds reduce thermal stress and are better for heat-sensitive materials, but they may leave behind residues if the laser energy isn’t sufficient. Effective scanning speed must be balanced with power and spot size—for example, a higher power laser may need to move faster to avoid overheating.
The interaction between these three parameters—power, spot size, and speed—is dynamic. Increasing one often requires adjusting the others to maintain quality and avoid unintended effects. Dialing in the correct combination requires understanding the material properties, contaminant characteristics, and desired surface finish. In high-quality continuous laser cleaning, precision in parameter selection isn’t optional—it’s essential.
Proper Equipment Setup and Maintenance
High-quality continuous laser cleaning doesn’t rely on laser parameters alone—it also depends heavily on the condition and setup of the equipment. A well-maintained system ensures consistent performance, minimizes downtime, and extends the life of critical components. Two key areas that directly impact cleaning quality are optical components and alignment and calibration.
Optical Components
The optics—such as lenses, mirrors, and protective glass—play a crucial role in delivering clean, focused laser energy to the surface. Over time, these components can accumulate dust, debris, or residue from the cleaning process itself. Dirty or damaged optics can scatter the laser beam, reduce power transmission, distort the beam profile, or cause uneven cleaning. Regular inspection and cleaning using proper tools (e.g., lint-free wipes, isopropyl alcohol, or dedicated optical cleaners) helps preserve beam quality. In environments with heavy contamination, protective windows or air knives should be used to shield optics from direct exposure to debris.
Alignment and Calibration
Misalignment of the laser beam or scanning head can lead to inconsistent cleaning patterns, reduced accuracy, and poor surface results. Even small deviations can shift the focal point, causing the beam to either miss the target area or deliver insufficient energy. Regular calibration ensures that the laser’s path is properly aligned with the target surface and that the beam focus is maintained at the correct working distance. This is especially critical in automated or robotic systems where repeatability is key. Calibration routines should be part of routine maintenance, using alignment tools like beam profilers, reference targets, or built-in software diagnostics.
Neglecting optical upkeep or system alignment can cancel out even the best parameter settings. By making equipment setup and maintenance a priority, especially focusing on clean optics and precise calibration, operators can maintain consistent beam quality, improve cleaning precision, and reduce the likelihood of costly rework. Clean optics and a properly aligned system are the foundation of reliable, high-quality continuous laser cleaning.
Optimal Focus Position
One of the most important factors in achieving high-quality results in continuous laser cleaning is maintaining the optimal focus position. The focus point is where the laser beam is most concentrated, delivering maximum energy density to the surface. If this point is not correctly aligned with the material being cleaned, the process becomes less efficient and can even damage the substrate.
When the laser is focused too far above or below the surface, the beam spreads out, reducing its intensity and precision. This leads to inconsistent cleaning, incomplete removal of contaminants, and in some cases, unwanted heating of surrounding areas. On the other hand, a properly focused beam ensures a sharp, controlled interaction with the target layer, removing contaminants cleanly without affecting the base material.
Maintaining optimal focus is especially critical in continuous laser systems, where the beam is active at all times. Even slight variations in the distance between the laser head and the work surface, due to uneven parts, vibrations, or misalignment, can degrade cleaning performance over time. To address this, many systems use auto-focus functions, height sensors, or precision calibration routines to keep the focus consistently accurate.
Regularly checking and adjusting the focus position not only improves cleaning quality but also increases process reliability and reduces the need for rework.
Effective Process Control
Maintaining high-quality results in continuous laser cleaning depends heavily on effective process control. This involves carefully managing key variables during operation to ensure the laser consistently removes contaminants without damaging the substrate. Two critical aspects of this control are consistent cleaning distance and uniform energy distribution.
Consistent Cleaning Distance
The distance between the laser head and the work surface—also known as the standoff or working distance—directly affects beam focus and cleaning effectiveness. If the distance varies during operation due to part geometry, vibration, or movement inaccuracies, the laser can lose focus, resulting in uneven or incomplete cleaning. In some cases, it can even damage the surface. To maintain a consistent cleaning distance, systems should be equipped with height sensors, auto-focusing mechanisms, or rigid fixturing that ensures stable part positioning. Robotic arms or gantry systems with feedback control can also help maintain precise distance on complex or curved surfaces.
Uniform Energy Distribution
For consistent cleaning across the entire surface, the laser beam must deliver energy evenly as it scans. Irregular energy distribution—caused by poor beam quality, scanner instability, or incorrect overlap—leads to streaks, patchy cleaning, or heat buildup. Using high-quality optics, properly tuned galvanometer scanners, and optimized path planning ensures smooth, even coverage. Overlapping scan lines at the correct rate also helps maintain uniform cleaning results across wider areas.
When these two factors—distance and energy uniformity—are kept under tight control, the laser cleaning process becomes more stable, predictable, and efficient. Effective process control not only improves surface quality but also minimizes rework, reduces waste, and extends equipment life.
Material Considerations
To improve the quality of continuous laser cleaning, understanding the material being treated is just as important as optimizing equipment and process settings. Both the base material and the type of contaminant influence how the laser should be applied. Tailoring the process to material-specific characteristics helps avoid damage, ensures complete contaminant removal, and maintains consistent results across different surfaces.
Base Material Properties
Different metals respond differently to laser energy. For example:
- Aluminum is highly reflective and has high thermal conductivity, meaning it reflects much of the laser energy and disperses heat quickly. This requires higher power levels or slower scanning speeds to achieve effective cleaning.
- Steel, being less reflective, absorbs laser energy more efficiently and is generally easier to clean with moderate power.
- Copper reflects even more than aluminum and requires very fine-tuned parameters to avoid energy loss or overheating.
- Titanium and other specialized alloys may require strict thermal control to avoid oxidation or surface discoloration.
The thickness and sensitivity of the material also matter. Thin sheets or delicate components can warp or deform under excess heat, so laser intensity and exposure time must be precisely controlled.
Contaminant Type and Characteristics
The nature of the material to be removed, whether it’s rust, oxide layers, oil, paint, or scale, directly affects the required energy input:
- Thick rust or corrosion may need multiple passes at high power with slower scanning speeds.
- Paint may blister or vaporize at lower energy levels, but can leave residue if the beam isn’t properly focused.
- Oil films or light oxides typically require less energy and faster scanning, but still need uniform coverage to avoid missed spots.
Layer thickness, adhesion strength, and chemical composition all play roles in determining the best process settings. Some materials may also release gases or particulates that affect the optical path or pose safety risks, requiring extraction systems or protective optics.
Surface Condition and Post-Cleaning Requirements
In many applications, the surface must meet specific standards after cleaning—for example, weld readiness, adhesion quality, or surface appearance. Laser cleaning must remove contaminants while preserving (or even improving) the surface finish. For instance, rough surfaces may require more energy to reach contaminants trapped in pits or irregularities, while smooth surfaces may need a tighter focus to avoid uneven cleaning lines.
In addition, certain applications require the base material’s surface texture or color to remain unchanged. This demands precise tuning of laser parameters to avoid microstructural changes, discoloration, or etching.
Effective continuous laser cleaning isn’t one-size-fits-all. Each material brings its own set of challenges and tolerances. The more you understand about the base material, the contaminant layer, and the surface requirements, the better you can tailor the process. By aligning laser parameters with specific material properties, you improve cleaning performance, protect the integrity of the workpiece, and reduce the risk of rework or damage.
Environmental and Safety Measures
Improving the quality of continuous laser cleaning isn’t just about fine-tuning equipment and settings—it also requires a safe, well-controlled working environment. Proper environmental and safety measures protect both personnel and equipment while ensuring consistent cleaning performance. Two critical areas to focus on are ventilation and fume extraction, and operator safety precautions.
Proper Ventilation and Extraction
Laser cleaning produces airborne contaminants, including dust, vaporized material, and microscopic particles. These byproducts can reduce visibility, contaminate optics, and pose health risks if inhaled. In some cases, such as when removing paint or coatings, harmful chemicals or heavy metals may also be released into the air.
To manage this, effective fume extraction and filtration systems are essential. Localized extraction units should be placed near the cleaning zone to capture emissions at the source. High-efficiency particulate air (HEPA) filters or activated carbon filters can help trap fine particles and chemical fumes. Good airflow and ventilation in the workspace further reduce airborne buildup and protect sensitive components from contamination.
Safety Precautions
Laser systems, especially continuous-wave units, pose significant safety risks if not handled properly. Direct or reflected laser beams can cause serious eye and skin injuries. All operators must wear appropriate laser safety goggles rated for the specific wavelength in use. Access to the cleaning area should be restricted during operation, using interlocked enclosures or physical barriers where possible.
Warning signs, emergency stop controls, and proper training are also essential parts of a safe setup. Additionally, operators should be aware of electrical hazards, moving parts, and hot surfaces within the system.
A clean, safe, and controlled environment contributes directly to consistent laser cleaning performance. By ensuring proper ventilation and extraction of fumes, and enforcing strict safety measures, you not only protect people and equipment—you also create the conditions necessary for high-quality, repeatable results in continuous laser cleaning.
Advanced Monitoring and Feedback Systems
As continuous laser cleaning becomes more integrated into automated manufacturing environments, advanced monitoring and feedback systems play a critical role in improving process quality and consistency. These technologies allow operators to track key performance metrics in real time, identify deviations, and make adjustments instantly, minimizing errors, reducing waste, and ensuring repeatable results.
Real-Time Monitoring
Modern laser cleaning systems can be equipped with sensors that monitor parameters such as beam intensity, surface temperature, reflectivity, and contamination removal rate. These systems use cameras, photodiodes, thermal sensors, or spectroscopy tools to evaluate how the laser interacts with the surface. For example, a thermal sensor can detect when too much heat is being applied to the material, triggering an automatic reduction in laser power to prevent damage.
Closed-Loop Feedback
Feedback systems close the loop between detection and control. Instead of waiting for human input, they automatically adjust process parameters—like scanning speed, beam focus, or power output—based on real-time data. This self-correcting approach improves reliability and minimizes variability caused by surface inconsistencies, part geometry changes, or fluctuating contamination levels.
Data Logging and Analysis
Continuous monitoring also enables long-term data collection. Analyzing this data over time helps operators identify performance trends, spot recurring issues, and refine cleaning recipes. Predictive maintenance can also be scheduled more accurately by tracking wear on optics, scanner drift, or laser power output degradation.
Advanced monitoring and feedback systems turn continuous laser cleaning into a smarter, more adaptive process. By detecting issues as they happen and automatically correcting them, these technologies raise the bar for cleaning precision, reduce rework, and ensure consistent surface quality—especially in high-volume or high-precision applications.
Operator Training and Expertise
No matter how advanced the equipment, the quality of continuous laser cleaning ultimately depends on the skill and knowledge of the operator. Well-trained personnel are essential for setting up the process correctly, responding to issues in real time, and optimizing cleaning performance based on the specific application. Without proper training, even the best system can deliver poor results or become a safety risk.
Understanding the Technology
Operators should have a clear understanding of how continuous laser cleaning works, including the interaction between laser parameters (power, spot size, scanning speed) and different materials or contaminants. They should also be familiar with how adjustments to focus, alignment, and distance affect cleaning quality. This technical knowledge allows operators to make informed decisions, rather than relying on trial and error.
Hands-On Skill Development
Beyond theory, operators need hands-on experience. This includes learning how to calibrate and align the system, perform basic maintenance, inspect optical components, and troubleshoot common problems. Training should also cover how to interpret monitoring data and adjust parameters for changing material conditions.
Safety Awareness
Operator expertise also includes strict adherence to laser safety protocols, such as proper use of protective eyewear, area controls, and emergency procedures. A safety-conscious operator not only protects themselves and others but also helps maintain a clean, controlled working environment that supports consistent results.
Investing in operator training isn’t optional—it’s essential. A knowledgeable, experienced operator is the first line of defense against quality issues and equipment misuse. By building strong technical skills and a clear understanding of the process, companies can maximize the performance of their continuous laser cleaning systems and maintain high standards across all applications.
Continuous Improvement Practices
Improving the quality of continuous laser cleaning isn’t a one-time effort—it requires ongoing evaluation, refinement, and adaptation. By adopting continuous improvement practices, manufacturers can consistently raise process efficiency, reduce defects, and stay aligned with evolving production needs. This approach involves collecting data, analyzing performance, and applying small, incremental changes that add up to meaningful gains over time.
Routine Process Evaluation
Regular reviews of cleaning performance help identify inconsistencies or opportunities for enhancement. This includes inspecting cleaned surfaces for uniformity, checking for incomplete contaminant removal, and monitoring cycle times. Small deviations in results often point to issues with laser parameters, optics, focus, or material variation—early detection prevents larger problems later.
Data-Driven Optimization
Collecting and analyzing process data allows for evidence-based improvements. Tracking metrics such as cleaning speed, energy consumption, error rates, and rework frequency reveals patterns and weak points. Using this data, operators can adjust laser settings, modify scanning strategies, or refine material handling methods to optimize results.
Feedback from Production Teams
Operators, technicians, and quality inspectors often have firsthand insights into recurring issues or process limitations. Encouraging feedback and cross-functional collaboration helps surface practical ideas for refinement, from fixture design improvements to changes in cleaning sequence or surface prep.
Adapting to New Materials and Requirements
As production demands evolve—new materials, tighter tolerances, or different contaminants—laser cleaning processes must adapt. Maintaining a mindset of experimentation and learning ensures the system can meet new challenges without sacrificing quality.
Continuous improvement is about building a culture of refinement. By routinely evaluating performance, using data to guide decisions, and staying responsive to new demands, teams can maintain high standards in continuous laser cleaning and push the process to deliver even better results over time.
Summary
Improving the quality of continuous laser cleaning requires more than just turning on the machine—it’s about controlling every element of the process. Continuous laser cleaning machines offer fast, precise, and environmentally friendly surface preparation, but achieving consistent, high-quality results depends on several key factors.
First, selecting the right laser parameters—power, beam spot size, and scanning speed—ensures efficient cleaning without damaging the substrate. Proper equipment setup and regular maintenance, especially of optical components and beam alignment, maintain system accuracy and performance over time. Keeping the laser focused at the optimal distance and ensuring even energy distribution across the surface are also essential for uniform results.
Material properties, such as reflectivity, thickness, and contaminant type, must guide process adjustments to prevent overheating or incomplete cleaning. A safe and controlled working environment, supported by reliable ventilation and adherence to laser safety protocols, protects both operators and equipment.
Advanced monitoring systems and real-time feedback help detect issues early and allow automatic adjustments for greater consistency. Trained operators with a solid understanding of the process can troubleshoot problems, fine-tune settings, and improve outcomes. Finally, continuous improvement—driven by data, routine evaluation, and adaptability—ensures the cleaning process evolves with production demands.
When all these elements are aligned, continuous laser cleaning can deliver clean, precise, and repeatable results at an industrial scale.
Get Laser Cleaning Solutions
Improving the quality of continuous laser cleaning starts with using the right equipment—and having the right partner. At Maxcool CNC, we specialize in the design and manufacturing of advanced continuous laser cleaning machines built for industrial performance, precision, and reliability. Our systems are engineered to meet the demands of high-speed, high-accuracy cleaning applications across a range of industries, including automotive, aerospace, shipbuilding, and heavy manufacturing.
Every production environment is different, which is why we offer tailored solutions based on your specific materials, contaminants, and cleaning requirements. Whether you’re removing rust, paint, oxides, or oil, our team works with you to configure the ideal combination of laser power, scanning system, and automation level. We also support our customers with expert consultation, on-site training, and full technical support to help you get the most out of your system.
In addition to high-performance machines, we provide advanced features such as real-time monitoring, automated focus control, and integration-ready platforms for robotic or inline cleaning setups. With Maxcool CNC, you’re not just getting a machine—you’re getting a complete solution designed to improve quality, efficiency, and long-term reliability.
Contact us to learn how Maxcool CNC can help elevate your continuous laser cleaning process with smart, scalable solutions built for your success.