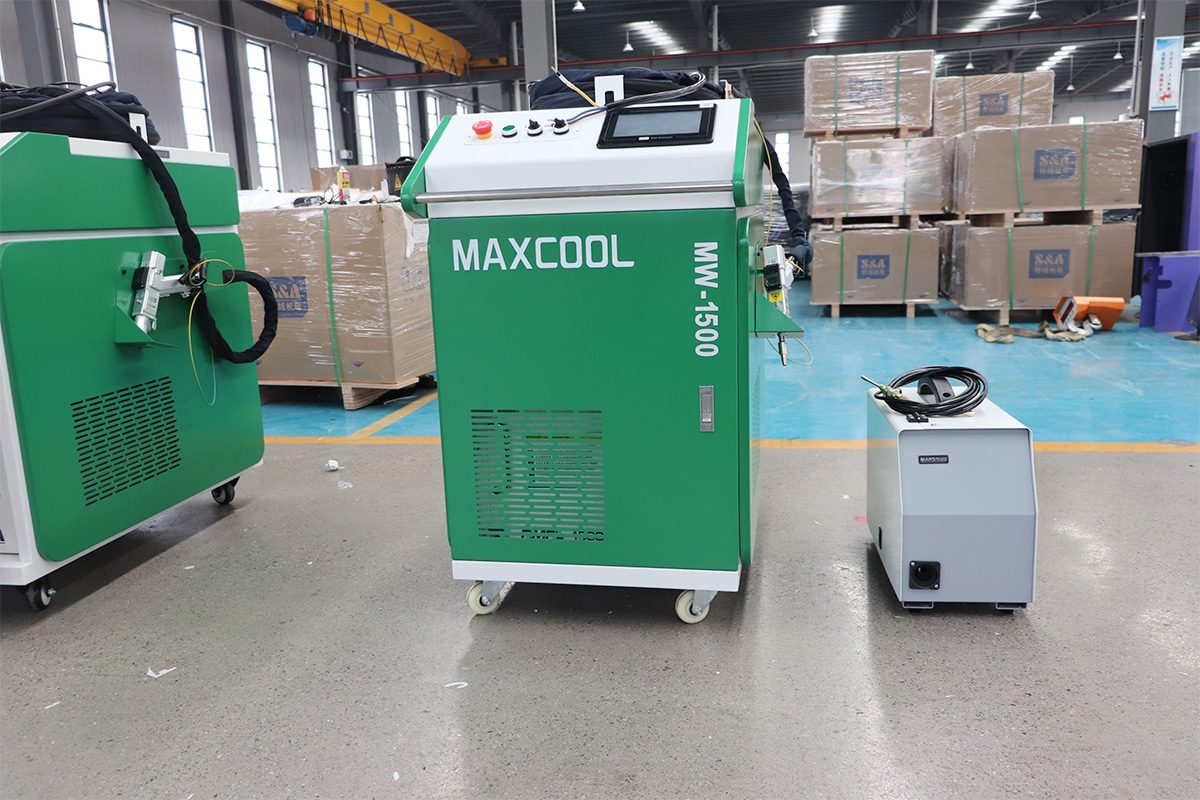
How Does Laser Welding Produce High-Quality Welds?
Laser welding is known for its ability to produce clean, precise, and high-strength welds, especially in industries where accuracy and quality are critical, such as aerospace, automotive, electronics, and medical device manufacturing. Unlike traditional welding methods that rely on electrical arcs or filler materials, laser welding uses a concentrated beam of light to generate intense heat, fusing metals with minimal distortion. This highly focused energy source allows for deep penetration, narrow weld seams, and fast processing speeds, even on complex or miniature components. As a result, laser welding has become the go-to solution for applications demanding both structural integrity and aesthetic finish. In this article, we’ll break down how laser welding works, what makes its welds superior, and why it’s often the preferred choice for precision manufacturing. Understanding the mechanics behind this process helps explain its growing role in modern fabrication and engineering.
Table of Contents
Laser Welding
Definition
Laser welding is a thermal joining process that uses a focused beam of high-intensity laser light to melt and fuse materials at their interface. The process is highly precise, making it ideal for joining small components or producing intricate welds in high-spec industries such as automotive, aerospace, electronics, and medical device manufacturing. Unlike conventional welding methods, laser welding typically does not require filler materials and results in minimal heat-affected zones, reducing the risk of warping or material degradation.
Working Principle
The core principle of laser welding lies in delivering concentrated energy to a specific area. A laser beam—usually in the infrared spectrum—is directed onto the material surfaces to be joined. The energy from the laser is absorbed, generating intense heat that causes rapid localized melting. Once the laser moves on or is turned off, the molten material quickly solidifies to form a weld.
Laser welding can operate in two main modes:
- Conduction Mode Welding: Used at lower power densities, the laser heats the surface without penetrating deeply. Heat conducts into the material, creating wider, shallower welds. This mode is useful when minimal penetration is acceptable and surface appearance is important.
- Keyhole Mode Welding: At higher power densities, the laser vaporizes a small portion of the material, creating a vapor cavity or “keyhole.” This cavity increases laser absorption, allowing for deeper, narrower welds with strong fusion. Keyhole welding is preferred for thick sections or applications requiring structural strength.
Laser welding is typically performed using computer-controlled systems, ensuring consistent beam positioning, travel speed, and power delivery.
Types of Laser Generators
There are three primary types of laser sources used in welding, each with unique characteristics suited to different applications:
Fiber Lasers
- Use an optical fiber doped with rare-earth elements (e.g., ytterbium) to generate the laser beam.
- Offer high electrical efficiency, excellent beam quality, and long service life.
- Suitable for deep, fast welds in metals like steel, aluminum, and titanium.
- Common in automotive and industrial applications due to their reliability and low maintenance.
CO2 Lasers
- Use a gas mixture (primarily carbon dioxide, nitrogen, and helium) as the laser medium.
- Emit long-wavelength infrared light (10.6 µm), which is better absorbed by non-metals but less effective for reflective metals.
- Capable of high-power output and are effective for welding thicker sections.
- Require mirrors for beam delivery and more frequent maintenance compared to fiber lasers.
Nd:YAG (Neodymium-doped Yttrium Aluminum Garnet) Lasers
- Use a solid-state crystal medium to produce laser light at 1.064 µm wavelength.
- Can operate in pulse or continuous mode, making them ideal for precision spot welding.
- Often used in medical, aerospace, and electronics manufacturing.
- Though largely being replaced by fiber lasers in many fields, they are still valued for specific micro-welding tasks.
Each generator type has its strengths and limitations, and the choice depends on the application’s material, thickness, desired weld quality, and production scale.
Laser Welding Process Parameters
Achieving high-quality welds with laser welding depends heavily on controlling key process parameters. Each parameter affects how the laser interacts with the material, influencing penetration depth, weld shape, and overall joint quality. The main factors include laser power, beam diameter, and focus, welding speed, and beam quality.
Laser Power
Laser power determines the amount of energy delivered to the workpiece. Higher power enables deeper penetration and faster welding, but increases the risk of defects like keyhole instability, spatter, or burn-through if not controlled properly. Low power may result in insufficient fusion. Matching the power to the material type and thickness is critical for a strong, defect-free weld.
Beam Diameter and Focus
The laser beam’s diameter at the focal point affects energy density. A smaller, tightly focused beam produces higher energy concentration, leading to deeper, narrower welds. However, it requires precise alignment. A larger beam reduces penetration and may increase the heat-affected zone. Proper focus position—ideally at or just below the surface—ensures consistent weld quality.
Welding Speed
Welding speed controls how quickly the laser moves across the joint. Faster speeds reduce heat input and minimize distortion, but if the speed is too high, the weld may be shallow or incomplete. Slower speeds increase penetration but can cause excessive melting or porosity. Optimizing speed ensures good fusion while preserving the base material’s properties.
Beam Quality
Beam quality refers to how well the laser can be focused to a small spot, often measured by the beam parameter product (BPP). A higher-quality beam (lower BPP) enables finer focus, deeper penetration, and greater precision. This is especially important for high-accuracy applications like electronics or medical device welding.
In short, maintaining tight control over these parameters is what allows laser welding to consistently produce strong, clean, and reliable welds—even on complex or miniature components.
Factors Affecting High-Quality Laser Welding
Several critical factors influence the ability of laser welding to consistently produce high-quality welds. These include the precision of heat application, penetration depth, cleanliness during processing, and the resulting metallurgical structure of the weld. Each plays a key role in ensuring the weld is strong, clean, and reliable.
Precision and Control
Laser welding offers exceptional control over the heat input, allowing for a narrow Heat-Affected Zone (HAZ). This minimizes thermal damage to the surrounding material and helps preserve the original dimensions of the workpiece. As a result, distortion and warping are significantly reduced, even in thin or sensitive materials. The high focus and accuracy of the laser beam make it ideal for applications that demand tight tolerances.
Deep Penetration Capability
With its high energy density, laser welding can efficiently weld thick materials in a single pass. This deep penetration ability not only increases productivity but also ensures uniform penetration depth, which is critical for structural integrity. Consistent weld depth eliminates internal voids or weak spots, leading to stronger, more reliable joints.
Cleanliness and Purity
Laser welding is a clean process by design. It produces minimal spatter and oxide formation, especially when performed in a controlled or shielded environment. This reduces contamination risks and leads to visually clean, high-strength welds. Minimal byproducts also reduce the need for post-weld cleaning or finishing.
Metallurgical Properties
The rapid heating and cooling cycles of laser welding result in a uniform microstructure within the weld zone. This controlled solidification enhances mechanical properties such as strength, fatigue resistance, and durability. With the right parameters, the weld can match or even exceed the mechanical performance of the base material.
By controlling these factors, laser welding delivers precise, strong, and high-quality welds that meet the demands of modern manufacturing and engineering applications.
Benefits of High-Quality Laser Welding
Laser welding offers a combination of precision, efficiency, and quality that sets it apart from traditional welding methods. When properly executed, high-quality laser welding delivers several key advantages that benefit both product performance and production efficiency.
Improved Mechanical Properties
High-quality laser welds result in joints with strong metallurgical bonding and a uniform microstructure. The precise heat control and rapid solidification help minimize internal stresses and defects, leading to enhanced strength, fatigue resistance, and overall durability. In many cases, the welded joint matches or exceeds the mechanical properties of the base material, making it suitable for demanding applications in aerospace, automotive, and medical manufacturing.
Cost Savings
While the initial investment in laser welding equipment can be high, the process offers significant cost efficiencies over time. It enables high-speed operation, reduces the need for filler materials, and minimizes rework thanks to its accuracy and consistency. Laser welding also generates little spatter or distortion, cutting down on post-weld cleanup and machining. When integrated into automated systems, it supports high-throughput production with reduced labor costs.
Enhanced Aesthetics and Surface Finish
Laser welds are known for their clean, narrow seams and minimal surface disruption. The precision of the process means less visible discoloration, smoother joints, and little to no need for additional finishing. This is particularly important in industries where appearance is a factor, such as consumer electronics, medical devices, or visible automotive components.
In short, high-quality laser welding not only ensures strong, reliable welds but also delivers tangible benefits in terms of efficiency, cost, and final product appearance.
Challenges and Considerations for Achieving High-Quality Welds
While laser welding offers many advantages, consistently achieving high-quality welds requires careful attention to several challenges and process variables. Poor setup, incorrect parameters, or unsuitable materials can compromise weld strength, appearance, and reliability.
Material Suitability
Not all materials respond equally well to laser welding. Highly reflective metals like copper and aluminum can reflect the laser beam, making them harder to weld without specialized equipment or techniques. Material thickness, thermal conductivity, and surface coatings can also affect weld quality and need to be evaluated beforehand.
Precision in Setup and Alignment
Laser welding is a high-precision process, and even small misalignments can lead to incomplete fusion, weak joints, or defects. Accurate part positioning, beam focus, and joint preparation are critical to ensure consistent results, especially for fine or micro-welding tasks.
Control of Process Parameters
Weld quality depends heavily on maintaining the right balance of laser power, focus, speed, and shielding gas. Variations in any of these can lead to issues such as porosity, cracking, undercutting, or excessive heat-affected zones. Tight process control and real-time monitoring are essential, especially in automated systems.
Equipment Cost and Maintenance
Laser welding systems require a significant upfront investment and regular maintenance to ensure reliability and performance. Beam delivery components, optics, and cooling systems must be kept in optimal condition. For some operations, this may require dedicated personnel or support.
Heat Management and Distortion Risk
Although laser welding generally causes minimal distortion, improper parameter settings or welding thick sections without preheating can still lead to thermal stress or warping. It’s important to plan for proper heat management, especially when welding complex assemblies.
Safety Considerations
Due to the high-intensity laser beam, safety is a major concern. Proper shielding, protective eyewear, and compliance with laser safety standards are essential to protect operators and maintain a safe working environment.
By addressing these challenges through proper planning, skilled operation, and consistent process control, manufacturers can fully leverage the benefits of laser welding while maintaining high weld quality.
Summary
Laser welding produces high-quality welds by combining precision, control, and efficiency. Using a concentrated laser beam, the process delivers deep, narrow welds with minimal heat input, reducing distortion and preserving the properties of the base material. Key process parameters—such as laser power, beam focus, welding speed, and beam quality—must be carefully controlled to ensure consistent, defect-free results. The ability to weld thick materials, generate minimal spatter, and maintain a clean, uniform microstructure gives laser welding an edge in demanding applications. Benefits include improved mechanical performance, lower production costs, and superior surface finish. However, achieving this level of quality requires careful material selection, precise setup, and ongoing equipment maintenance. Despite these challenges, laser welding continues to be the method of choice in industries that demand strength, precision, and aesthetics. By understanding how laser welding works and what factors influence its performance, manufacturers can unlock its full potential in advanced fabrication.
Get Laser Welding Solutions
For manufacturers seeking reliable, high-performance laser welding systems, Maxcool CNC offers advanced solutions tailored to your production needs. As a professional manufacturer of laser welding machines and laser cleaning machines, Maxcool CNC delivers equipment built for precision, durability, and ease of integration. Whether you’re working with fine components or heavy-duty materials, Maxcool’s machines are engineered to provide deep penetration, minimal distortion, and consistent weld quality across a wide range of applications. With a strong focus on innovation, quality control, and customer support, Maxcool CNC helps businesses improve efficiency, reduce waste, and elevate the quality of their products. From initial consultation to after-sales service, Maxcool provides comprehensive support to ensure you get the most out of your investment. If you’re ready to enhance your welding capabilities, trust Maxcool CNC to deliver cutting-edge laser solutions that meet the demands of modern manufacturing.