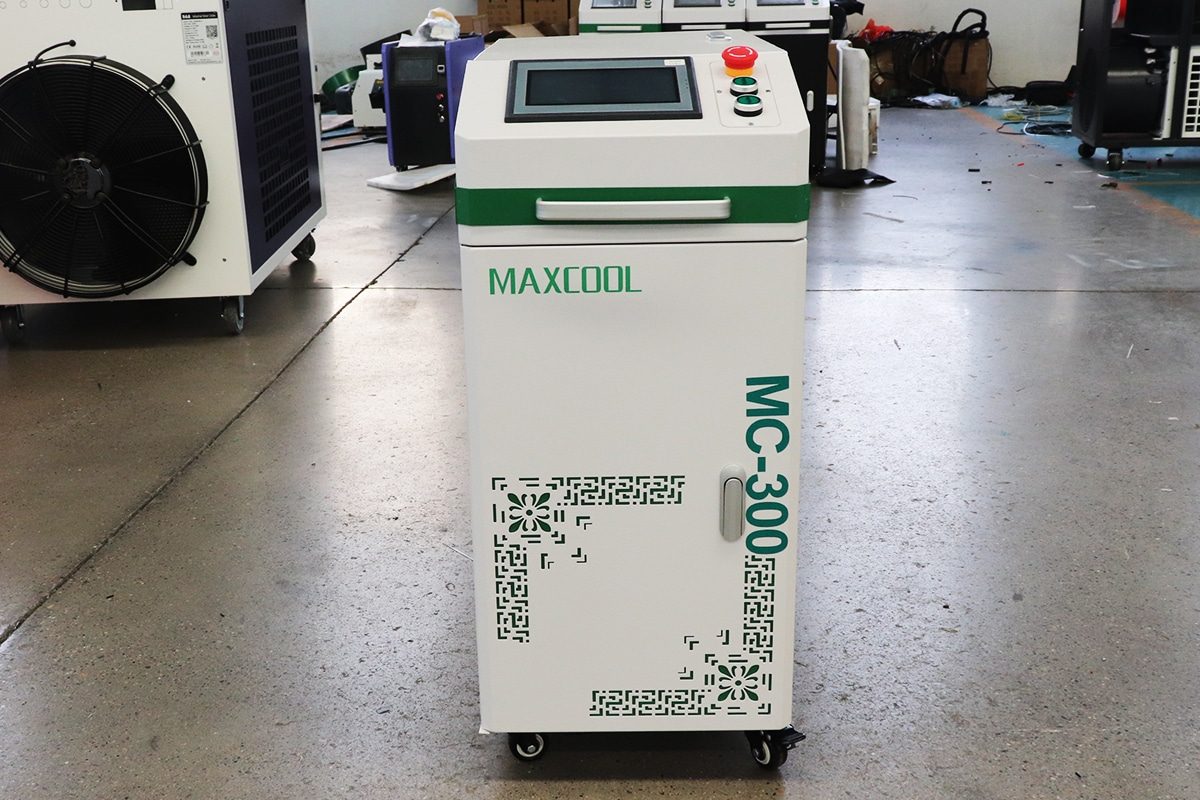
Does Pulsed Laser Cleaning Damage The Substrate?
Pulsed laser cleaning has emerged as a powerful method for removing contaminants, oxides, coatings, and residues from a wide range of surfaces. Unlike traditional mechanical or chemical cleaning techniques, it offers precise, non-contact treatment with minimal environmental impact. However, as its use expands in industries like aerospace, electronics, cultural heritage preservation, and automotive manufacturing, a critical question remains: Does pulsed laser cleaning damage the underlying substrate?
This concern is central to the adoption of the technology, particularly when working with delicate materials or components that require precise tolerances and surface integrity. Damage to the substrate can compromise structural performance, electrical conductivity, or visual aesthetics, depending on the application. While pulsed lasers allow fine control over parameters like energy density, pulse duration, and repetition rate, the boundary between effective cleaning and surface alteration isn’t always clear-cut.
This article examines whether and how pulsed laser cleaning can damage substrates, identifies the factors that influence this risk, and guides users can mitigate it. By understanding the interaction between laser energy and material properties, we can better assess when this cleaning method is safe and when it might do more harm than good.
Table of Contents
Fundamentals of Pulsed Laser Cleaning
Pulsed laser cleaning operates by directing short, high-energy laser pulses onto a surface to remove unwanted layers without damaging the underlying material. The process hinges on the precise interaction between laser parameters and the physical properties of both the contaminant and the substrate. A deep understanding of the underlying mechanisms is essential for evaluating the potential for substrate damage.
Pulse-Duration Regimes
Laser pulses can range from nanoseconds (ns) to picoseconds (ps) and femtoseconds (fs). Each regime affects the cleaning process differently. Nanosecond lasers are common and suitable for many industrial applications, but tend to produce more thermal effects. Picosecond and femtosecond lasers offer ultra-fast energy deposition, leading to “cold” ablation with minimal thermal diffusion. The shorter the pulse, the more confined the energy transfer, reducing the chance of substrate heating and damage.
Energy Deposition & Ablation
The laser energy is absorbed by the contaminant or surface layer, causing rapid heating, expansion, and ultimately, material ejection—known as ablation. The efficiency of ablation depends on the absorption properties of the layer and the laser wavelength. Ideally, the contaminant absorbs more energy than the substrate, allowing selective removal. Improper energy settings can cause insufficient cleaning or, worse, damage the underlying material through excessive energy absorption.
Heat-Affected Zone (HAZ)
Even in pulsed laser cleaning systems, some thermal diffusion can occur. The heat-affected zone refers to the region of the substrate where temperature rise alters the material’s microstructure or properties. Nanosecond pulses are more likely to produce a noticeable HAZ, while ultrashort pulses can limit this effect. Controlling pulse parameters is key to minimizing thermal impact and maintaining substrate integrity.
Threshold Fluence and Selectivity
Every material has a threshold fluence—the minimum energy per unit area required to initiate ablation. Cleaning is most effective when the contaminant’s threshold is lower than the substrate’s. This differential allows selective removal. However, exceeding the substrate’s threshold can lead to etching, melting, or other forms of degradation. Selectivity is achieved by careful tuning of laser fluence, pulse overlap, and scanning speed.
Pulsed laser cleaning is a highly controllable process, but the line between effective cleaning and substrate damage is defined by a combination of pulse duration, energy deposition, thermal effects, and material thresholds. Understanding and managing these factors is crucial for ensuring that the cleaning process is efficient, selective, and safe for the substrate.
Damage Mechanisms in Theory and Practice
While pulsed laser cleaning is designed to be a non-invasive surface treatment, damage to the substrate can still occur through several distinct mechanisms, each linked to how laser energy interacts with matter. Understanding these mechanisms is critical to assessing risk and designing processes that avoid unintended consequences. Theoretical models and experimental studies have identified multiple pathways through which damage can develop.
Thermal Melting
When laser energy exceeds the thermal capacity of the substrate, localized melting may occur. This is especially common in metals and polymers with relatively low melting points or in cases where nanosecond pulses allow time for thermal diffusion. Melt zones can disrupt surface finish, dimensional tolerance, and mechanical properties. Even brief melting can lead to recrystallization, roughening, or alloy segregation upon resolidification.
Shock-Wave Microcracking
High-intensity pulses can generate shock waves that propagate into the material. Brittle substrates like ceramics or glass are especially vulnerable. These pressure waves can cause internal stresses, leading to microcracks, delamination, or even complete fracture. Microcracking may not be visible initially, but can compromise long-term structural integrity or lead to premature failure in service.
Plasma Sputtering and Redeposition
At higher fluences, ablation generates a plasma plume that can eject particles at high velocities. These ejected materials can redeposit unevenly on the surface or nearby components, creating unwanted residues or embedding debris into the substrate. Redeposition may introduce contamination, alter optical or conductive properties, or increase surface roughness.
Photochemical Bond Scission
In cases where ultrashort pulses or UV lasers are used, photochemical interactions may dominate. These can break molecular bonds directly without significant heating. While this allows for clean ablation of organic contaminants, it can also modify or weaken polymeric or organic substrates at the molecular level, changing their chemical structure or surface energy.
Oxidative Flash Heating
Laser interaction in an ambient environment can lead to rapid oxidation due to sudden surface heating. This is particularly problematic for metals prone to oxidation, like aluminum or copper. Oxidative flash heating can form brittle oxide layers, change surface reflectivity, or reduce corrosion resistance. The presence of oxygen, humidity, or reactive gases amplifies this risk.
Residual Stress and Hardening
Rapid heating and cooling from pulsed laser exposure can induce residual stresses in the substrate. In metals, this may lead to hardening through microstructural changes or phase transformation. While sometimes desirable, these changes can also lead to distortion, stress-corrosion cracking, or fatigue issues if not properly controlled.
Substrate damage during pulsed laser cleaning can arise through multiple mechanisms: thermal, mechanical, chemical, and structural. The risk depends on laser parameters, environmental conditions, and material properties. To prevent such damage, process optimization must account for these variables, balancing cleaning efficiency with substrate safety. A theoretical understanding combined with practical experimentation is essential for developing robust, damage-free laser cleaning protocols.
Experimental Evidence of Substrate Damage
Though pulsed laser cleaning is widely promoted as a precise and safe technique, real-world experiments and case studies reveal that substrate damage is possible—and sometimes inevitable—depending on the material, laser parameters, and cleaning goals. Across various industries and research domains, controlled experiments have documented specific types of damage in metals, composites, cultural-heritage materials, semiconductors, and carbon steels. These findings highlight the need for tailored laser settings and rigorous post-cleaning analysis.
Metals
In metals like aluminum, copper, and titanium alloys, damage typically takes the form of thermal melting, oxide layer formation, and surface roughening. Experiments show that exceeding the threshold fluence even slightly can cause melting pits or discoloration. Surface morphology studies via SEM (Scanning Electron Microscopy) often reveal microstructural changes, grain boundary etching, and redeposition effects. High-repetition-rate nanosecond lasers, in particular, are prone to generating cumulative thermal stress if not carefully tuned.
Composites
Fiber-reinforced polymer composites are highly sensitive to laser exposure due to the differing thermal and optical properties of the fiber and matrix. Research indicates that laser cleaning can cause matrix degradation, fiber exposure, delamination, and even interfacial debonding. Femtosecond lasers help reduce thermal damage, but care must still be taken to avoid affecting the fiber orientation and mechanical integrity of the composite.
Cultural-Heritage Stone & Artworks
Stone monuments, frescoes, and historical sculptures have been treated with pulsed lasers for decades, especially in conservation contexts. While successful in many cases, documented issues include surface whitening, microcracking, and changes in porosity or mineral phase due to overheating or shockwave stress. Tests on marble, limestone, and polychrome surfaces show that even short-pulse lasers can alter the patina or pigment layers if the fluence isn’t precisely calibrated.
Semiconductor Wafers
Silicon wafers and semiconductor devices require extremely high surface precision. Experimental work has revealed that pulsed lasers can induce unwanted doping effects, surface amorphization, or even lattice damage under improper conditions. These changes, while sometimes subtle, can alter electronic behavior, reduce yield, or introduce reliability risks. Studies emphasize the importance of ultra-short pulse durations and minimal thermal load to preserve wafer quality.
Carbon Steel
In industrial settings, carbon steel is frequently cleaned prior to coating or welding. However, pulsed laser cleaning can lead to surface oxidation, grain coarsening, and hardening due to rapid heating. Hardness testing post-cleaning often reveals significant increases in surface hardness, which, while useful for wear resistance, can also lead to brittleness and microcrack initiation under stress.
Experimental data across material classes confirm that pulsed laser cleaning is not inherently risk-free. Metals can melt, composites can delaminate, heritage artifacts can discolor, semiconductors can malfunction, and carbon steel can harden unpredictably. The type and extent of damage vary by substrate and laser parameters, underscoring the need for thorough testing, adaptive control systems, and material-specific cleaning protocols to ensure damage-free operation.
Process Parameters That Control Damage
The likelihood of substrate damage during pulsed laser cleaning is closely tied to how the process is configured. Each laser parameter plays a role in determining whether the material is effectively cleaned, partially altered, or irreversibly damaged. Fine-tuning these variables—individually and in combination—is essential to ensure safe, efficient cleaning tailored to specific substrates and contaminants. Below is a breakdown of the most critical parameters influencing damage potential.
Fluence (J/cm²)
Fluence, or energy density, is arguably the most influential parameter. It must be high enough to ablate the unwanted layer but not so high that it affects the underlying substrate. Surpassing the substrate’s threshold fluence can cause thermal melting, microcracking, or oxidation. Controlled cleaning typically operates just above the contaminant’s ablation threshold and below that of the substrate, maintaining selectivity.
Pulse Width (τ)
The duration of each pulse affects how the laser energy interacts with the surface. Longer pulse widths (nanoseconds) allow more time for heat diffusion, increasing the risk of a heat-affected zone (HAZ). Shorter pulses (picoseconds or femtoseconds) deposit energy more rapidly, minimizing thermal transfer and enabling “cold ablation.” Selecting an appropriate pulse width is critical for sensitive or thin materials.
Repetition Rate
The number of pulses delivered per second (Hz) impacts how quickly heat accumulates. A high repetition rate can lead to heat buildup, even if individual pulses are non-damaging. Cumulative thermal effects are especially problematic on metals and semiconductors. Lower repetition rates or active cooling between passes can help manage temperature rise.
Beam Overlap (%)
Beam overlap determines how much one laser spot overlaps with the next during scanning. While high overlap improves cleaning uniformity, it also increases local energy exposure. Excessive overlap can lead to overprocessing and substrate degradation. Optimal overlap balances thorough coverage with controlled energy input—typically 30–70%, depending on application.
Wavelength
The wavelength affects how deeply the laser penetrates and how selectively it is absorbed. Shorter wavelengths (e.g., UV or green) are absorbed more readily by surface contaminants and certain polymers, enabling precise ablation with minimal substrate interaction. Infrared wavelengths may penetrate deeper, increasing the risk of bulk heating. Matching the wavelength to the absorption properties of the contaminant improves selectivity and minimizes substrate risk.
Assist Gas
Assist gases such as nitrogen, argon, or compressed air can help by cooling the surface, removing ablated particles, and suppressing oxidation. For metals, inert gases are preferred to prevent flash oxidation. Improper gas flow or type, however, may lead to redeposition or inconsistent cleaning. Assist gas selection should be based on substrate chemistry and cleaning objectives.
Incident Angle
The angle at which the laser beam strikes the surface influences how energy is distributed. A perpendicular (normal) angle delivers the highest intensity, but oblique angles can help reduce penetration depth and control energy coupling. Angled incidence is often used for delicate surfaces or textured geometries to spread energy and reduce hotspot formation.
Substrate safety during pulsed laser cleaning hinges on meticulous control of process parameters. Fluence, pulse width, and repetition rate directly influence how energy is delivered and dissipated. Beam overlap, wavelength, assist gas, and incident angle shape the energy’s spatial and chemical effects. Mastery of these variables enables precision cleaning while minimizing the risk of thermal, mechanical, or chemical damage to the substrate.
Application-Specific Risk Profiles
The risk of substrate damage from pulsed laser cleaning is not uniform across industries—it varies significantly depending on the materials involved, the cleanliness requirements, and the performance tolerances of each application. From aerospace to cultural heritage preservation, each field faces unique challenges in balancing cleaning effectiveness with substrate integrity. Understanding these application-specific risk profiles is essential for developing safe and reliable laser cleaning protocols.
Aerospace
In aerospace, laser cleaning is used for preparing surfaces for bonding, removing corrosion, or stripping coatings from high-value components like turbine blades or structural alloys. The risk profile here is high: even slight surface damage can compromise fatigue resistance, aerodynamic performance, or structural integrity. Titanium and aluminum alloys are sensitive to thermal input, making tight control of fluence and pulse duration essential. Non-uniform ablation or microcracks can have catastrophic consequences in flight-critical parts.
Automotive
Laser cleaning in the automotive sector is often applied to weld pre-treatment, rust removal, and mold cleaning. Compared to aerospace, the risk tolerance is slightly broader, but damage can still affect weld strength, coating adhesion, or part longevity. Steel substrates may experience surface hardening or residual stress if parameters are not carefully managed. The use of automated systems with moderate fluence and precise scanning helps reduce variability and maintain production quality.
Electronics
In electronics manufacturing, pulsed laser cleaning is employed to remove oxides, residues, or micro-contaminants from delicate components like printed circuit boards (PCBs), connectors, or semiconductor wafers. The risk profile here is extremely high. Even minimal substrate modification can lead to conductivity loss, insulation breakdown, or thermal performance issues. Ultrafast lasers (picosecond or femtosecond) are typically preferred to ensure damage-free, low-thermal cleaning with high spatial precision.
Cultural Heritage
Conservation of artwork, stone monuments, and historical artifacts relies on laser cleaning for its ability to remove black crusts, pollutants, or overpainting without mechanical abrasion. However, the materials involved—marble, limestone, pigments—are fragile and often irreplaceable. The risk is not just structural but aesthetic and historical. Excess energy can whiten stone, alter pigments, or create microcracks. Extremely low fluence, careful wavelength selection, and rigorous pre-testing are standard practice in this domain.
Nuclear Decontamination
In nuclear facilities, pulsed lasers are increasingly considered for removing radioactive surface layers from steel, concrete, and painted structures. Here, substrate damage is often secondary to thorough decontamination. However, excessive melting, spatter, or redeposition can create new waste challenges or compromise structural components. The presence of radiation adds complexity, requiring remote monitoring and control. A balance must be struck between aggressive cleaning and containment of ablated material.
Each application domain comes with its own set of risks and tolerances for pulsed laser cleaning. Aerospace and electronics demand ultra-precise control to avoid compromising critical performance. Automotive and nuclear sectors allow slightly higher energy use but still require strict management to prevent unintended consequences. Cultural heritage preservation demands the utmost care to protect delicate and irreplaceable surfaces. Tailoring the laser process to fit the specific risk profile of each field is essential for achieving effective, damage-free results.
Economic & Environmental Implications
Beyond technical performance, pulsed laser cleaning offers distinct economic and environmental advantages, though not without trade-offs. Understanding these implications is crucial for evaluating the true cost-benefit profile of the technology. While the potential for substrate damage remains a concern, when managed properly, pulsed laser cleaning can reduce long-term operating costs, environmental impact, and downtime in ways that traditional methods cannot match.
Reduced Consumables
One of the most immediate benefits is the elimination or drastic reduction of consumables. Unlike abrasive blasting, chemical stripping, or solvent-based cleaning, laser systems do not require media, detergents, or hazardous chemicals. This cuts recurring supply costs and reduces storage, disposal, and handling requirements. Fewer consumables also translate into a cleaner, safer workspace and simplified regulatory compliance, especially in industries where environmental regulations are strict.
Capex vs. Continuous-Wave (CW) Systems
Pulsed laser systems tend to have a higher upfront capital expenditure (Capex) compared to continuous-wave lasers. This is due to the complexity of pulse generation, cooling systems, and control electronics. However, the greater precision and reduced risk of thermal damage often make pulsed systems a better fit for high-value or sensitive applications. In sectors like aerospace and electronics, the higher CapEx is justified by lower rework rates, extended part life, and improved process quality.
Cycle-Time Savings
Despite their higher unit cost, pulsed lasers can deliver significant cycle-time advantages. Faster material removal with minimal masking, preparation, or post-cleaning processing translates to shorter turnaround times. Automated systems can clean complex geometries or targeted areas more efficiently than manual methods. Over time, the reduction in downtime, labor, and throughput bottlenecks can lead to substantial productivity gains, especially in manufacturing and maintenance settings.
Energy Use
Energy efficiency is another key factor. Pulsed lasers are more energy-intense per pulse than CW lasers, but they use that energy in shorter, more controlled bursts. This precision often means less overall energy is needed to remove a given contaminant layer. When compared to energy-hungry abrasive blasting systems or ovens used in thermal cleaning, pulsed lasers may offer better efficiency, especially when optimized for the material and task. Furthermore, the lack of waste materials or ventilation demands contributes to a smaller environmental footprint.
Pulsed laser cleaning can provide strong economic and environmental benefits, including lower consumable costs, faster cleaning cycles, and reduced waste. While the upfront investment is typically higher, especially compared to CW lasers or conventional methods, the long-term savings in operational efficiency and sustainability often outweigh the initial cost. When combined with careful control to avoid substrate damage, pulsed laser cleaning becomes not only a technically viable option but also a cost-effective and eco-conscious solution.
Summary
Pulsed laser cleaning is a powerful, precise, and environmentally friendly surface treatment technology—but it is not without risks. While it offers significant advantages over traditional cleaning methods, such as reduced chemical use, lower consumable costs, and minimal physical contact, the potential for substrate damage remains a critical consideration. Thermal melting, microcracking, plasma redeposition, and chemical alterations can all occur if the process is poorly controlled or misapplied.
The key to avoiding damage lies in understanding and managing the complex interaction between laser parameters and material properties. Variables such as fluence, pulse width, repetition rate, beam overlap, wavelength, and the use of assist gas must be carefully optimized. Best practices—like pre-testing on coupons, using inert gases, and employing multi-pass strategies—can dramatically reduce risk.
Application-specific factors also play a major role. High-performance industries such as aerospace, electronics, and cultural heritage conservation demand extreme precision and minimal surface alteration. Others, like automotive or nuclear decontamination, tolerate slightly higher risk for the sake of speed and efficiency.
Ultimately, when properly applied, pulsed laser cleaning can deliver exceptional results without damaging the substrate. Success depends on careful planning, process discipline, and a deep understanding of both the materials and the technology involved.
Get Laser Cleaning Solutions
Choosing the right laser cleaning system is critical to achieving effective, damage-free results, and that starts with partnering with a trusted provider. AccTek Group is a professional manufacturer of intelligent laser equipment, offering advanced pulsed laser cleaning solutions tailored to a wide range of industries and materials. Whether you’re working with delicate aerospace alloys, intricate electronics components, or historic cultural artifacts, AccTek Group systems are engineered for precision, efficiency, and safety.
Our laser cleaning solutions are built with industry-leading control technology, enabling precise adjustment of fluence, pulse width, repetition rate, and scanning patterns. This allows users to fine-tune the process for maximum cleaning performance without exceeding substrate damage thresholds. Features such as real-time temperature monitoring, assist gas integration, and programmable multi-pass strategies are designed to ensure both effectiveness and material protection.
AccTek Group offers expert consultation, on-site testing, and custom equipment configuration to match your specific cleaning challenges. From manual handheld systems to fully automated robotic platforms, our solutions scale with your needs while reducing costs, environmental impact, and operational downtime.
If you’re considering pulsed laser cleaning and want to ensure substrate safety without compromising performance, AccTek Group is your go-to partner. Contact us today to explore how our intelligent laser systems can meet your toughest cleaning requirements.